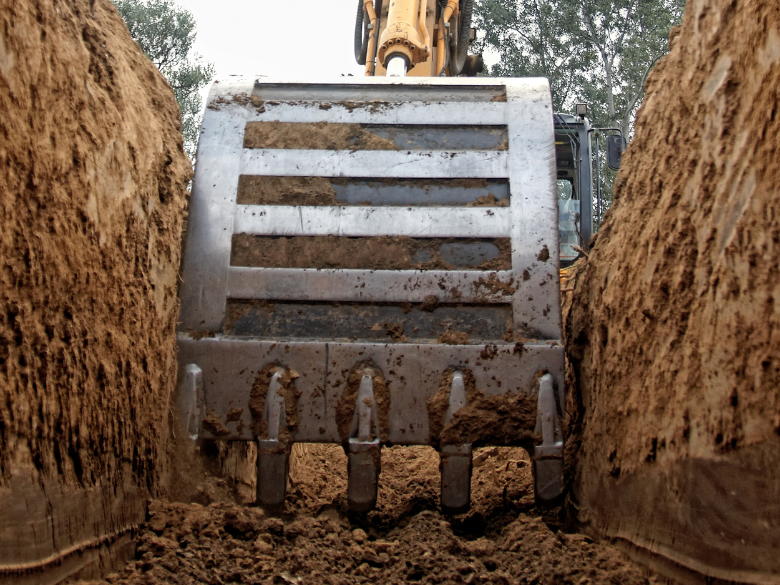
Working with heavy machinery and managing traffic on-site can be risky. But with the right checks and planning, we can keep everyone safe.
Before starting work each day, make sure your equipment is ready to go:
Visual checks (before starting the machine):
Stationary function test (with the machine on):
Moving function test:
Using your manufacturer’s checklist or the HazardCo Heavy Machinery Prestart checklist can help you cover all these points.
Keeping vehicles and people safe on-site requires a solid traffic management plan. Here’s what to consider:
Discuss this plan during site inductions so everyone knows the rules and expectations.
Heavy machinery can affect the stability of excavations if operated too close. Keep all heavy vehicles, materials, and spoil at least one meter outside the zone of influence unless specific designs support closer operations.
Uneven ground can cause machinery to tip over, leading to serious injuries. To prevent this:
If you would like more information head over to our website or to chat with one of our friendly Advisory team please give us a call on 1800 954 702.
Digging into the ground might seem straightforward, but excavation work is actually one of the most dangerous parts of construction. That’s why it’s important to plan ahead and put the right safety measures in place to keep everyone safe on site.
Before you get started, take some time to plan things out. Planning involves identifying the hazards, assessing the risks, and deciding suitable controls — all with input from the team. Every site is different, so take its unique features into account.
Keeping yourself and your team safe is what matters most. Make sure you’re clear on your responsibilities when it comes to managing excavation risks.
Need a hand? The HazardCo App has helpful resources for site reviews and risk controls. And if you’ve got questions or need support, just reach out to the HazardCo team – we’re here to help.
When you’re able to get back on site after a flood or storm, here are the hazards, risks and control measures you should consider to help reduce the risk of injury and illness to yourself, your workers and others involved in the clean up and repair effort.
Dust is a common hazard in the construction industry, especially during demolition or refurbishment. When buildings are demolished they can release materials that create hazardous dust (airborne contaminants) which can be hazardous to workers’ health. Understanding the risks will help you to identify how best to manage the risks.
Why is dust dangerous?
Exposure to hazardous dust can lead to serious health conditions, including:
Health and exposure monitoring
As a business, you have a duty to monitor your workers’ health when they’re exposed to certain substances and other hazardous materials. Regular health monitoring helps identify early signs of illness and ensures that the dust control measures in place are working effectively.
Health monitoring process should include:
It is important that you get your worker’s consent to monitor their health and engage them in this process.
Health monitoring should be carried out by a trained and competent person. They will also give recommendations based on the health monitoring results.
How to control dust exposure on-site
Controls to minimise the exposure to dust in the workplace could include:
Making sure your workers have the right tools and information to complete the job safely includes training and understanding the risks involved, what to do if anything should go wrong, as well as the correct use, storage, and maintenance of PPE.
Other controls to consider are:
Complete a SWMS for your demolition work through the HazardCo APP. This helps assess the risks and plan safe work processes. Involve your team so everyone can contribute and understand the plan.
Our team of health and safety experts are just a call away if you have any questions or would like to discuss further.
The holiday season is over and now it’s time to get back into the swing of things. Coming back to work and reopening your site is just as important as shutting it down. The New Year is the perfect opportunity to refocus and set the tone for the year ahead. Coming back to work after a couple of weeks off can give some people a serious case of Mondayitis, so consider taking the following steps on the first day back:
Rather than diving straight into work, start with a kick-off toolbox talk. This is an essential step to rebrief your team on the SSSP (Site-Specific Safety Plan), emergency procedures, and Safe Work Method Statements (SWMS). Use this time to check that all workers are fit for work and mentally prepared after the break.
Perform a site review to identify any new hazards or potential risks that may have emerged during the downtime. Check that fences are still secure and containers are locked.
After a break, it’s crucial to ensure all structures and scaffolds are intact. Inspect scaffolds, check excavations, and assess other infrastructure that may have been affected by weather conditions during your time off. Ensure everything is in working order before resuming normal operations.
Before use, inspect all tools and equipment to confirm they are in good condition. It’s also vital to pre-start mobile plant to ensure it’s functioning correctly.
Consider a soft start to your operations. Allow your team the time to properly check their work areas, inspect equipment, and remind everyone that safety is the number one priority. This includes keeping in mind workers don’t overheat after spending the last couple of weeks in air conditioning, relaxing, and indulging. They may not be acclimatised to working in the heat.
As the weather heats up, so can risk on-site. Make sure that workers are provided with adequate protection from working in the heat so that they can do their work safely and comfortably. Here are some steps to help mitigate these risks:
If temperatures are dangerously high, it’s sometimes best to stop work until conditions improve. Consider shifting physical tasks to machinery for tasks such as lifting or digging, reducing the exposure to extreme heat.
Safety is a shared responsibility. Encourage your team to keep an eye on each other and to report any symptoms of heat stress. Prevention is key, but swift action can prevent more severe conditions from developing. For the early stages of heat-related illness, first aid can often be effective, but you should always seek medical assistance if in doubt, or if the person’s symptoms are severe.
Symptoms to look out for are:
Be prepared this summer and make sure to keep the health, safety, and well-being of workers front of mind. Refer to the below resources for more information:
If you have any questions you can contact our Advisory Team on 1800 954 702.
The holiday season is almost upon us, and we’re all eager to have a bit of a rest, recharge, and spend quality time with our families. As we wind up 2024, it is a demanding time for construction as we try to complete jobs before the holiday shutdown. This can make it tempting to take shortcuts, however, it can also lead to an increase in incidents, with the last two months of the year seeing a spike in workplace incidents.
Common factors can include time pressure, working in the heat, and fatigue. It’s important to keep the health, safety, and well-being of workers front of mind.
It’s necessary to start preparing for the Christmas shutdown so that you don’t have any interruptions during your break or come to a nasty surprise on your first day back. This is particularly important with residential sites which are mostly in populated areas.
Unsecured sites could be hazardous to members of the public, especially children, particularly with sites near parks, schools, homes or recreational areas. Children are unaware of the dangers of a construction site so keeping them out is key.
Download our Site Security Checklist for a comprehensive list.
Taking the time to prepare your site for the holiday shutdown can help to make sure you get to spend uninterrupted time with your family and friends.
If you have any questions or would like to discuss your Health and Safety please give our Advisory Team a call on 1800 954 702 or email info@hazardco.com.
We hope you have a safe and enjoyable break over the holiday season!
Electricity is essential on construction sites, but if the risks are not managed properly, it can pose serious dangers to people and property. Proper controls must be in place wherever electricity is used to keep everyone safe.
Because we use electricity differently across a site there are different ways to help manage the risks.
An RCD is an electrical safety device designed to immediately switch off the supply of electricity when electricity ‘leaking’ to earth is detected at harmful levels. RCDs offer high levels of personal protection from electric shock.
Fixed at the switchboard
Built into the powerpoint
Portable
Keep you and your team safe while working around electricity by checking your RCD regularly. Across Australia, the testing frequency is based off the standard, AS/NZS 3012:2019 which sets the specific requirements for construction sites and states:
If an RCD is tested and found to be faulty it must be taken out of service immediately and replaced as soon as possible.
Leads and cords are easily damaged, particularly those connected to equipment that is often moved. To protect them:
Inspection, testing and tagging of electrical leads and cords on construction sites are required to be completed every 3 months* by a competent person.
Any lead or cord that is damaged or that fails testing is to be immediately taken out of use and removed offsite. If you cannot promptly remove it offsite, consider other means like attaching a durable out of service tag so as to warn workers not to use that piece of equipment.
When you complete your regular Site Reviews using the HazardCo App, make sure that you are checking RCD’s and all other electrical equipment are in good working condition and are regularly inspected and tested.
If you have any questions in regards to this topic or need more support , reach out to HazardCo and speak to one of our expert Health and Safety Advisors. You can contact us on 1800 954 702.
*For Hire equipment, inspection is required prior to each hire and testing is carried out at least monthly. If hire equipment remains on the construction site then the frequency listed applies.
Health and safety is a core part of any business but incidents and injuries on the job can still happen. According to SafeWork Australia, in the construction industry alone there were 15,877 serious work-related injury claims between 2020 and 2021, and in the same period, there were 316 fatalities.
Construction and trades make up a fair portion of incidents and injuries at work. When you think about the cost of the time off, it adds up to a pretty staggered sum. As of 2020 the average compensation claim looks like:
With numbers like this, we need to help you find a way to improve the health and safety culture so you can make sure it’s safe and profitable as well.
The signs of poor health and safety
If you’re concerned that your health and safety policies and procedures aren’t being followed or maybe not quite up to scratch, there are a number of things you can keep your eyes peeled for:
So, how do you get your crew on board?
When it comes down to it, creating a culture of site safety isn’t as easy as putting new procedures in place and calling it a job well done – it’s up to you to involve and motivate your crew to be proactive and take safety into their own hands. You need to make sure that your crew are on board and are taking the right steps to create a safety culture.
Some steps you can take include:
Communication
It seems like an obvious one but poor communication can really hinder your efforts to create a safety culture. Having regular honest and open communication with your crew about why you’re talking about all things safety is the best way to help them understand the importance.
The more transparent and clear you are, the more likely they will be to really take the new initiatives seriously. Make sure that your crew has easy access to your current health and safety guidelines so they can stay in the know about any changes.
Support your staff
Site safety isn’t just about incidents on your site, it’s also about being a supportive employer who ensures their people are feeling safe and secure when they come to work every day. Make sure that the physical health, mental health and even emotional health of your people is a factor for how you manage them. Those working in construction and trades like other sections of society are at risk of depression, stress, or anxiety as well.
If you are taking steps to improve your site safety culture, make sure you factor in both physical and mental health awareness in all that you do for your staff. By providing resources and establishing an environment where your crew feels respected and safe to open up and express themselves you’ll be able to create a support system where you can look after each other’s wellbeing and mental health.
Training
Ensuring that your crew are trained up on all the correct licenses, procedures and health and safety practices is a sure fire way to make sure that they are fully knowledgeable on correct procedures. With the right training in place, you can have confidence that they know how to safely and correctly perform their jobs.
Be a leader
We’ve all experienced bad leadership before, and that if they don’t care about something, it’s highly unlikely you will either. So, if your crew sees that you don’t take health and safety seriously, you’re out of luck getting them to foster a culture of site safety.
You need to walk the walk before you talk the talk. Demonstrate to your crew the importance of following health and safety standards by doing them yourself. They’re a whole lot more likely to follow your example than just take your word for it.
Reporting
You need to set the tone with your crew that reporting incidents isn’t something they need to feel anxious or uncomfortable about doing. Make it clear that they won’t get in any trouble for making a report but instead see it as a way of finding out what caused the accident or injury and what can be done to make sure it won’t happen again. By making proper reporting a core element of your crew’s job responsibilities it can become second nature to them.
Make it a team effort
Site safety impacts everyone, so it makes sense that your crew should have a hand in shaping their site’s culture. The more input they have, the more likely they are to follow precautions.
By having regular health and safety chats with your crew, you can give them the opportunity to voice their own safety concerns and opinions. By having open conversations and allowing input from your crew you’re giving them the ability to implement safety measures that affect their own jobs, ultimately making them more likely to follow processes and encourage others to do the same.
If you have any questions please reach out to the HazardCo team today
You’re probably across the recent engineered stone ban, but did you know SafeWork Australia has just come out with new rules to further protect workers from crystalline silica found in other building materials? These new rules begin on 1st September this year and apply to all states except Victoria whose rules are already in place.
Crystalline Silica Substances (CSS) include stuff like sand, stone, concrete, and mortar that contain at least 1% crystalline silica. When you cut, crush, drill, polish, saw or grind these materials, they release tiny dust particles called respirable crystalline silica (RCS). These particles are so small they can get deep into your lungs, which can lead to serious health issues, like silicosis—a lung disease.
If silica dust is generated, assess if the work is high-risk. Document this using the handy Form in the HazardCo Hub, and if you determine the work is not high risk, you must explain why. If you’re unsure, assume it is high-risk. When assessing if processing CSS is high risk, consider these factors:
Eliminate or minimise the risks from processing the CSS as much as possible and use at least one of the following measures during the processing:
If workers are still at risk of being exposed to silica dust after you’ve put one or more of the above controls in place they need to be provided with respiratory protective equipment (RPE) and wear the respiratory protective equipment while the work is carried out.
Avoid high-risk tasks when possible. If unavoidable, create a silica risk control plan outlining tasks, risks, and controls. This plan must be developed with workers, shared with them before starting work, and regularly reviewed for effectiveness.
What needs to be in a silica risk control plan?
Keep it simple and easy to understand—no need for lengthy explanations.
We suggest using the SWMS tool in the HazardCo App if the processing creates a contaminated atmosphere or involves high-risk construction work. Just ensure all the Silica Control Plan requirements are covered.
Ensure that any worker involved in or at risk of RCS exposure due to high-risk CSS processing receives crystalline silica training. This training must be nationally accredited or approved by the WHS regulator and should cover health risks and the correct use of control measures.
Conduct air monitoring if you’re unsure whether silica levels exceed the Workplace Exposure Standard (WES) or need to assess if there are health risks from RCS processes. Hire a certified expert like an occupational hygienist, to perform the monitoring and ensure it meets standards. If levels exceed limits, report it to the Regulator within 14 days. Keep records for 30 years and make them available to affected workers.
Provide health monitoring for workers at significant risk from ongoing silica exposure, including those near high-risk processing. Keep records for 30 years and give a copy to the worker.
Regularly review safety measures, especially after workplace changes.
If you need guidance, reach out to our advisory team at 1800 954 702 for assistance.
HazardCo understands that on-site first aid is about more than just sending someone on a course every few years. As an employer or principal contractor on-site, you have a legal and moral obligation to make sure your team has access to first aid equipment and facilities, as well as access to trained first aiders.
To determine the necessary level for your workplace, assess the site by considering:
Don’t forget to involve your workers in the process and if you are working with multiple trades, or are the principal contractor, you should share information and work together cooperatively.
Having a first aid kit on a construction site is essential to quickly address injuries and medical emergencies. Great kits can be sourced from many places – a basic kit should include equipment t to tend to:
Basic first aid kits are not always enough given the nature of construction work and increased risk of eye injury, cuts, falls etc, so you’ll need to consider what other equipment to add e.g. eye pads, eyewash, additional dressings and bandages.
Include your team and see if they think your first aid kit is sufficient for the site hazards and team size… and make sure they know who the trained first aider is and where the first aid kit is kept! It helps if your first aid kit is clearly labeled and is made from a material that can protect the contents from dust, moisture and contamination.
Lastly, assign someone to be in charge of replenishing the kit. Make sure this happens regularly and keep a list of what’s supposed to be in the kit to make topping it up easier. At the same time, check training is up to date for your first aiders, and if your team size has changed, whether you still have enough team members trained in first aid.
Keeping first aid up to date is the right thing to do by your team, so make sure you’ve got things covered and that you’re all prepared if any sort of injury takes place.
If you have any questions please contact the HazardCo team today.