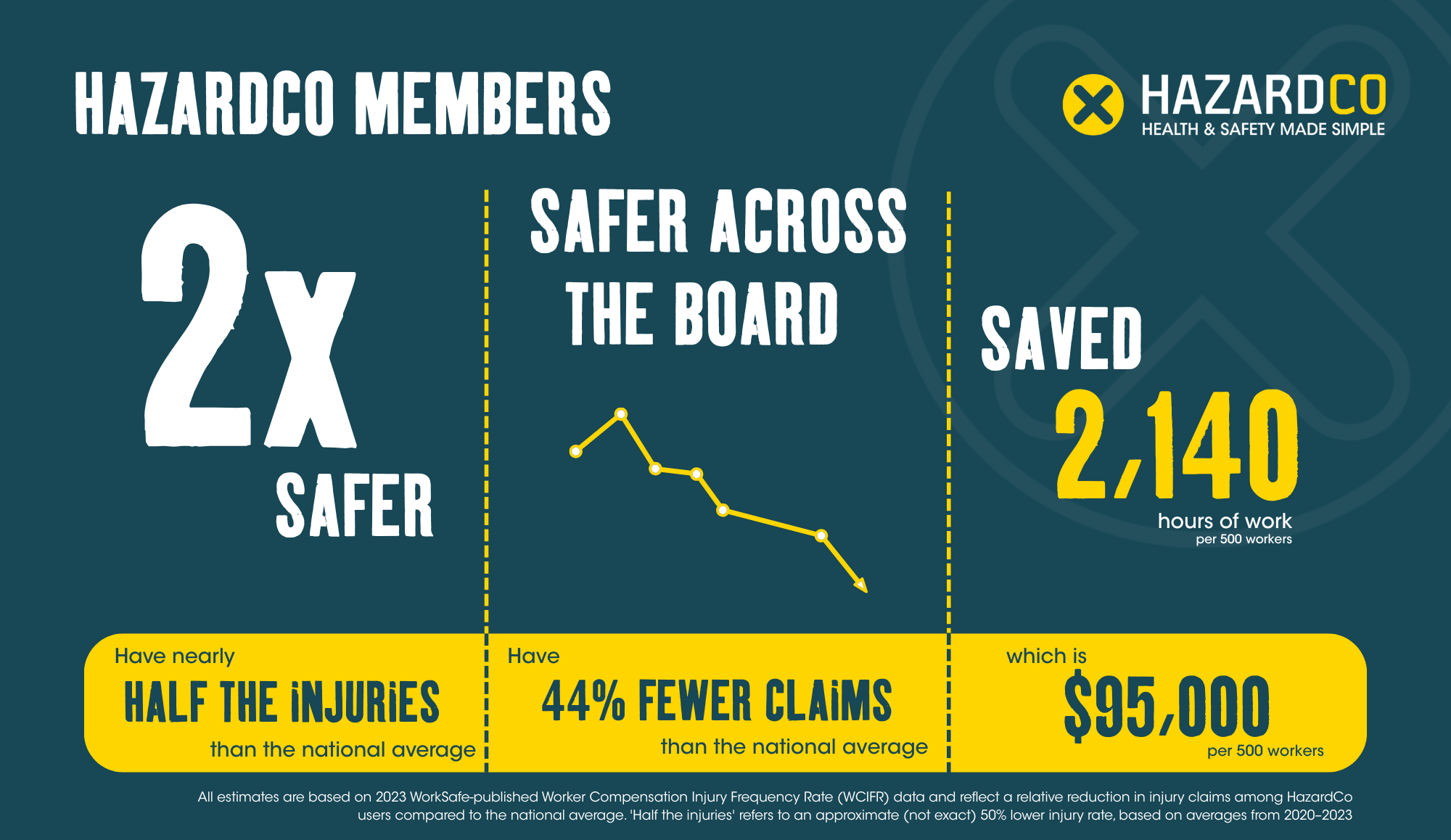
At HazardCo, we’re all about making health and safety simple – and it’s working. New data shows that our members are safer on site compared to the national average. Whether you’re on the tools or managing a team, these numbers show the real impact of doing health and safety the HazardCo way.
There’s a big difference between having a health and safety system and using one that actually works.
At HazardCo, we don’t just help you tick boxes. Our guided tools make it easy to follow the right health and safety steps at the right time — and when that happens, sites are safer. Now we’ve got the data to back it up.
New stats show that HazardCo members are significantly safer on site than the national average. Whether you’re on the tools or running the business, this proves that doing health and safety the HazardCo way pays off.
We’ve crunched the numbers and here’s what we found:
That’s a massive difference.
Why it’s working
Our digital tools make it easy to manage health and safety day to day. From guided Site Reviews that help you put the right controls in place, to risk assessments, toolbox talks, site inductions, SWMS and incident reports — it’s all handled in the HazardCo App.
Everyone on site can get involved, making it easier to spot risks early, take action, and keep things running smoothly. Plus, if something does go sideways, our expert advisors are available 24/7 to help you respond the right way.
When health and safety is easy to follow and part of your everyday routine, it becomes second nature – and it keeps people safer.
Fewer injuries mean less time off the tools, and that saves your business money. When your team stays safe, you avoid costly downtime, keep your jobs on track, and reduce the chance of needing to bring in extra workers to cover.
You’ll also be in a better position if the Regulator (Worksafe / Safework) ever comes knocking. HazardCo helps you meet your legal responsibilities and show you’re doing things properly, without the paperwork pile-up.
A well-run site is a safer site. It’s better for your crew, your schedule, and your bottom line.
Using HazardCo isn’t just about ticking boxes faster, it’s about making your site genuinely safer.
You’re working smarter, with fewer accidents, less downtime, and more time getting the job done right.
Our mission is to keep the person at the top of the ladder safe, and the data shows it’s working.
Not a member yet? Maybe it’s time to make the switch.
We get it — figuring out what to do after an incident or near miss on-site can feel a bit overwhelming. One of the most common things our Advisory Team hears is, “Do I need to report this?”If it’s a notifiable incident, you have a legal duty to let your State Regulator know – Sounds like a lot of paperwork right? Not with HazardCo, our App makes it easy to log an incident or near miss and we’re here to guide you with what to do next!
If someone needs immediate medical treatment for a serious injury, someone’s health and safety was put at serious risk, it might be classed as a notifiable incident. When you report it through the App, we’ll let you know if you need to report it.
Every time you report an incident or near miss, you’re helping make the site safer. It’s not about pointing fingers — it’s about learning from what happened and stopping it from happening again. Everyone on-site has the right to know about any risks, and we all play a part in keeping each other safe.
Creating a culture where everyone feels comfortable reporting issues means better communication and fewer surprises.
It’s easy:
Your report is saved in the Hub and kept on file while you’re a HazardCo member
What happens next?
The App will prompt you to give us a call if needed. Our Advisory Team gets a copy and will:
We recommend:
Keep records
You’re legally required to keep these records for at least 5 years. Logging everything in the App means it’s all saved in the Hub, organised and easy to access if you ever need it.
No one wants accidents to happen on site, but being prepared makes all the difference. Stay calm, follow the steps, and give us a call if you’re unsure. Our Advisory team is available 24/7 for serious incidents.
Got a question? Reach out to us today — we’re here to help.
Hand and finger injuries are one of the most common injuries on-site. Over the last year, HazardCo has received 4599 incident reports – 720 of those were hand or finger injuries. That highlights just how often these injuries happen, so let’s look at how they happen and what we can do to prevent them.
There are plenty of ways hands and fingers can get hurt on-site, but the most common injuries include:
These injuries happen due to faulty equipment, falling objects, getting caught between materials, electrical issues, and simple mistakes.
Many hand and finger injuries occur from everyday tools such as hammers, planes and utility knives, and handling metal sheets. There have also been an increasing number of injuries from nail guns. These injuries are often caused by rushing, fatigue, complacency, using damaged tools, or not having the right training.
Hand injuries aren’t just painful – they affect your ability to work and go about your daily life. Even minor injuries can weaken grip strength and finger movement. More serious injuries could mean permanent damage or loss of function.
Keeping hands safe is all about awareness and good habits. Here’s how you and your team can reduce the risk:
Safety isn’t just about following the rules. It’s about actions and leading by example. Leaders set the tone by demonstrating safe practices, sharing real stories of how hand injuries can impact lives and actively monitoring worksite conditions. Once workers understand the risk, it’s their responsibility to stay aware, but team leaders must make sure safety measures are in place and consistently followed.
Let’s work together to bring those hand injury numbers down!
Got a question about hand safety or any other health and safety issue? The HazardCo Advisory Team is here to help – call 1800 945 702
Anything with wheels and an engine should be at the forefront of your mind on site.
From delivery trucks to excavators, if it moves, and it’s got some weight… then that means power! it’s going to cause some damage if it isn’t controlled. So always keep safety in mind!
Keep pedestrians and vehicles apart
Separate the two wherever you can with careful planning at the design and set up stages.
Minimise vehicle movements
Provide car and van parking away from the work area if possible. Also control entry points, and plan storage areas, so that vehicles don’t need to cross the site where people are.
Turning and reversing vehicles
A spotter wearing high-vis clothing should guide the driver who can’t see clearly behind their vehicle. Mirrors, reversing, warning alarms, sensors and cameras can also make all the difference.
People on-site
When untrained workers drive vehicles without authority, you’re in trouble. Always manage the training and access of drivers to your vehicles, including those visiting.
Visibility
The more the better, just make sure it stands out in the right way. From on-site lighting to aids for drivers (mirrors, CCTV cameras and reversing alarms) to hi-vis clothing for those on the ground. Find out more about the use of hi-vis clothing on-site in our blog here.
Accidents are preventable when risk is managed. How do you manage risk? You get a plan – a good one.
A traffic management plan documents and helps explain how risks will be managed. This might include details of:
Every site is different, but your plan should be monitored and reviewed regularly. It should also be adapted when there are changes to your work situation.
If you have any questions get in touch with the HazardCo team today
We’re excited to announce that HazardCo is officially expanding into the UK! As a New Zealand-born company, we’ve been helping builders and tradies keep their worksites safe since 2007. Now, after years of growth and success in both New Zealand and Australia, we’re ready to bring our trusted health and safety system to the UK market.
Why HazardCo?
At HazardCo, we’re all about making health and safety simple. We know that builders don’t want to spend their time buried in paperwork or worrying about compliance. That’s why we offer digital tools and expert advice to make health and safety easy to manage on-site, in real-time. Whether it’s inductions, risk assessments, or creating safety plans, our system takes the hassle out of health and safety, so builders can focus on what they do best—getting the job done.
Our journey so far
We started in New Zealand, helping Kiwi builders tackle their health and safety challenges. Word spread fast, and soon we had thousands of businesses using our system to stay safe. In 2020, we expanded to Australia, growing to 70 employees and over 10,000 members, including more than 150,000 users actively managing on-site safety through our app.
What’s next?
Now, we’re bringing the same proven system to the UK. We’ve tailored our offering to meet the specific needs of British builders, and our local health and safety experts are ready to provide the support you need. With the recent introduction of the Building Safety Act, there’s never been a more important time for builders to step up their safety game—and we’re here to help make that as simple as possible.
As the construction industry moves toward more digital solutions, HazardCo is ready to help UK builders stay compliant, protect their teams, and keep projects running smoothly.
Ready to take the guesswork out of health and safety? We’ve got your back!
The HazardCo App has a new Plant/Machinery Pre-Start tool! It’s a quick and easy way to do pre-start checks on various plant and machinery such as scissor lists, boom lifts and excavators. Just whip out your app, follow the guided prompts and you’ll know all your reports are saved for safe keeping.
This is a great new tool for those of you currently filling in the log book that stays with the machine, causing lots of painful admin work to gather and compile the information for your own records.
Why conduct pre-start checks?
Pre-start checks are a simple way to check your plant and machinery is up to scratch before it’s used. Whether it’s hired or owned equipment, a quick check will help you to find any potential issues that could impact on the safety of your team or the performance of the machinery. By referring to the manufacturer’s instructions and best practices, workers can make sure the machinery they have is in a safe condition to be used, and if not, the App gives you an easy way to communicate the issues happening on the ground to the right people. When done well pre-start checks go a long way to preventing incidents and equipment failures.
When to use the Plant/MachineryPre-Start tool
The Plant/Machinery Pre-Start tool should be used before the operation of any plant or machinery. You can find it in the main menu of the HazardCo App. Once a pre-start check is completed, the report is automatically saved to the Reports section in the Hub and the App for easy access in the future.
Bennefits for workers: The Plant/Machinery Pre-Start tool provides an easy way to follow pre-start procedures. It helps you to communicate any issues that need to go up the chain and make sure information isn’t lost or misunderstood.
Benefits for workers: This tool is a quicker and easier way to maintain evidence of your crews safe work practises on site. Anyone on site can use the app to complete a Plant/Machinerypre-start, you’ll be able to see it’s been done, and you won’t need to find and scan physical log books anymore!
In light of the recent changes to Australia’s industrial manslaughter laws, we sat down with Glenn, one of our HazardCo Health and Safety (H&S) experts to break down what these laws mean for building companies and tradies.
Q: Glenn, what exactly is industrial manslaughter?
Glenn: Industrial manslaughter is a big deal because it means that if a business owner or someone in charge of a worksite doesn’t take safety seriously, and it leads to a worker’s death, they could be held legally responsible. It’s about accountability. If you knew—or should’ve known—that what you were doing (or not doing) could seriously harm someone, and it ends up causing a death, then we’re talking about industrial manslaughter.
Q: So what’s new with these laws? How are they different from before?
Glenn: The big change here is that industrial manslaughter is now a criminal charge—meaning individuals can face serious charges, and potentially be convicted and face prison time if found guilty. It’s a clear message that safety is non-negotiable. With South Australia and NSW putting in place industrial manslaughter laws this year, and Tasmania pending, they will soon be nationwide.
Q: Who does this law apply to? Is it just for business owners?
Glenn: While business owners are definitely in the spotlight, this law can apply to anyone who has a duty of care on a worksite. So if you’re in a position where you’re responsible for other people’s safety, and your negligence causes a fatality, you could be held accountable. It’s not just about the big bosses; anyone with responsibility for safety needs to be on their game.
Q: Can you give us some examples, Glenn, of how this duty of care might play out on a construction site?
Glenn: Absolutely. In construction, there are plenty of scenarios where this duty of care comes into play. For example, if a site supervisor gives wrong information, tools, or instructions, and a worker is killed, that site supervisor could be facing a charge of industrial manslaughter. It’s the same for contractors—say one builds faulty foundations, and someone ends up getting hurt or worse, that contractor could also be held responsible. And it doesn’t stop there; the PCBU (Person Conducting a Business or Undertaking) might also be on the hook if they didn’t have solid processes in place to ensure the build was up to standard.
Q: What constitutes industrial manslaughter, Glenn? What are the criteria for being charged?
Glenn: To be charged with industrial manslaughter, a few key things need to line up.
First, you have to be a PCBU or an officer of the PCBU.
Second, you must have engaged the individual to work on your site.
Third, you need to be aware of the safety risks they were exposed to.
Fourth, you didn’t do anything about those known risks—whether it’s changing, communicating, or documenting them.
And finally, a fatality has to occur as a result of those risks that you were aware of and failed to address. The main thing that really seals the deal here is what’s called “gross negligence.” Legally, it means that if you have a duty of care, know about a risk, and don’t take action, it becomes much easier to prove negligence. It’s not just about being aware of the risk; it’s about failing to act on it.
Q: This all sounds pretty serious, Glenn. Should businesses be worried?
Glenn: It’s serious, but there’s no need to panic if you’re doing the right thing. The key takeaway is that these laws are here to protect workers. If you’re following safety protocols, keeping your worksite safe, and not cutting corners, then you’re on the right track. The law is only a threat to those who ignore their responsibilities. It’s about doing what’s right, not just for the law, but for the safety of everyone on site.
Q: What steps can businesses take to avoid being charged with industrial manslaughter?
Glenn: There are five simple steps that can really help you stay on the right side of the law—and more importantly, keep everyone safe.
If you have any questions get in touch with the HazardCo team today
Maintaining clean amenities is just as important as keeping your site nice and tidy. Employers have a duty to provide adequate workplace amenities/facilities, including toilets, that are in good working order, clean, safe and accessible.
Not meeting these requirements can lead to a risk of infection, disease, psychosocial harm or infringements/enforcement from the Regulator. Regulators often actively check work sites to ensure workers have access to clean and safe amenities.
When planning amenities on your site, consult with your workers to understand what will be needed. Getting them involved will give you the opportunity to provide information, training and instruction on things like keeping the site amenities clean and reporting any problems.
More often than not portable toilets are not maintained in a safe or hygienic way. Employers must make sure that toilets are cleaned and serviced regularly, and, just like plant and other on-site equipment, safe to use and operated the way it was designed to be used.
Toilets should also:
Don’t forget, the toilet should be easy to access in all weather conditions and be placed on stable, flat ground to ensure it can operate properly.
Clean drinking water must be supplied to workers by installing site water taps as early as possible. If the mains have not been connected, provide workers with drinking water in containers, coolers or flasks.
Workers should have a clean and weatherproof area for meals and rest breaks. Using the garage or a similar sheltered area can be used and be set up as soon as possible. If they aren’t available on-site, workers should be given enough time on their breaks to access eating facilities off-site. Facilities should also include:
In the early stages of construction a worker can use their vehicle for shelter until a suitable area becomes available.
As always, if you have any questions please give our team a call on 1800 954 702 or contact us.
It’s important for young people starting out in construction to understand how to stay safe at work. Young workers lack experience and might not know about all the hazards yet, which could put them in danger of getting hurt. Sometimes young people might feel like they have to impress others, or they might think they’re better at the job than they actually are, they may also forget about safety rules or be afraid to speak up if something seems unsafe. Because of this young workers have additional needs and should be supervised when working on-site.
Positive safety culture onsite comes from the top down, supervisors should be actively modeling and training young workers about safety rules, make sure they have the right gear, and encourage them to speak up if they see any problems.
There are some jobs that young workers shouldn’t do because they might not have enough experience or strength yet. Supervisors need to make sure young workers can handle their tasks and keep an eye on them until they are sure they are able to do the work safely. Young workers also need to think about their own safety, listen to instructions and follow safety rules.
When everyone works together to stay safe, it helps make sure everyone goes home safely at the end of the day.
Now, let’s delve deeper into some specific measures that can be taken to ensure the safety and well-being of young workers in the construction industry:
Employing young workers in the construction industry has benefits for the young person, the company and for the industry as a whole as the next generation of builders learn and grow into future roles. By prioritising safety and investing in the well-being of young workers, employers can create a culture of safety that benefits everyone involved. Together, we can build a safer and more secure future for the next generation of construction workers.
If you have any questions, get in touch with the HazardCo team today
When you are renovating, you will most likely be working with others, such as the client or other contractors on-site. This means that you will need to think about how you will manage health and safety on-site and how you will communicate this with other people involved with the project. This will ensure that everyone is on top of the site hazards and practicing good health and safety during your renovation.
Here are a few things you will need to think about for your upcoming renovations:
Inductions are a way of ensuring workers and clients are aware of the risks and hazards that are involved in the job at hand, conducted at the start of each new job.
It is important that you induct your clients prior to starting the job, advising them about the health and safety guidelines that need to be followed for your work area, even when it’s their home.
If your work site is occupied by a client, or the client is likely to visit, then we recommend that you carry out the following:
Firstly, check the following three COVID-19 related questions with your client:
If the answer is yes to any of these questions, then the work should not commence.
Next, meet the client at the worksite (if possible) and explain the following:
Some good rules to use are:
These steps will help to identify the risks that you will be bringing into your clients home, because when health and safety is top of mind – your site is a safer place for everyone involved.
If you are working alone we suggest that you set up a procedure to regularly contact someone throughout the day to check-in that you are safe.