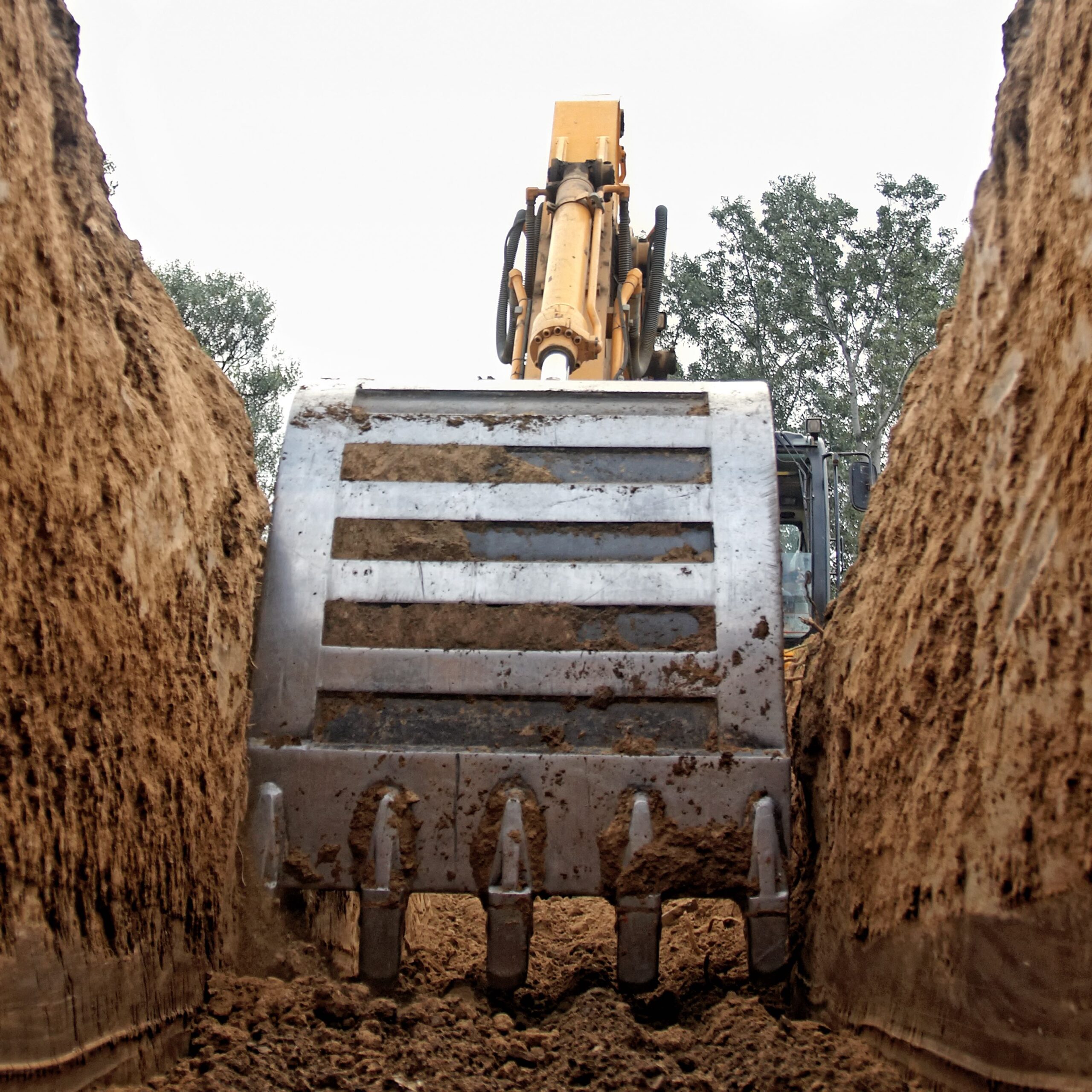
Working with heavy machinery and managing traffic on-site can be risky. But with the right checks and planning, we can keep everyone safe.
Before starting work each day, make sure your equipment is ready to go:
Visual checks (before starting the machine):
Stationary function test (with the machine on):
Moving function test:
Using your manufacturer’s checklist or the HazardCo Heavy Machinery Prestart checklist can help you cover all these points.
Keeping vehicles and people safe on-site requires a solid traffic management plan. Here’s what to consider:
Discuss this plan during site inductions so everyone knows the rules and expectations.
Heavy machinery can affect the stability of excavations if operated too close. Keep all heavy vehicles, materials, and spoil at least one meter outside the zone of influence unless specific designs support closer operations.
Uneven ground can cause machinery to tip over, leading to serious injuries. To prevent this:
If you would like more information head over to our website or to chat with one of our friendly Advisory team please give us a call on 0800 555 339.
Operating Machinery
Working with heavy machinery can be dangerous. Incorrect use or untrained operators can lead to serious injuries or worse.
Training and Supervision
Machinery should only be used by workers who are:
Regularly assess operator competency through refresher training, observations and feedback. Keep training records and verify workers have the appropriate licenses.
Before using any machinery, complete a daily prestart check. These checks must be done by a trained and competent person.
Visual checks (before turning the machine on):
Stationary test (machine is on but not moving):
Moving test (short drive):
Use the manufacturer’s pre-start checklist, the HazardCo Heavy Machinery Prestart Checklist or the HazardCo App Plant/Machinery Pre-start tool to guide your checks. Making sure to keep a record of your completed checks.
Quick Hitches, Safety Locks, and Exclusion Zones – Take the time to get it right
Quick hitches help you swap attachments fast – but can be dangerous if not properly secured.
Before operation:
All quick hitches must clearly show:
Store spare locking pins with the machine, and only use attachments that match the correct pin size.
Cover any machinery risks and controls in your task analysis and share it with everyone on-site.
Don’t cut corners on safety
Missing a step like skipping a daily check or rushing an attachment change can have serious consequences.
Taking five minutes to do it right can prevent serious injuries and keep your sire running safely.
If you have any questions, get in touch with the HazardCo Team today
Digging into the ground might seem straightforward, but excavation work is actually one of the most dangerous parts of construction. That’s why it’s important to plan ahead and put the right safety measures in place to keep everyone safe on site.
Before you get started, take time to plan things out. Planning means identifying the hazards, assessing the risks, and deciding suitable controls – with input from the team. Make sure an emergency plan is in place in case something goes wrong. Every site is different, so take its unique features into account when planning.
Keeping yourself and your team safe is what matters most. Make sure you’re clear on your responsibilities when it comes to managing excavation risks.
Need a hand? The HazardCo App has helpful resources for site reviews and risk controls. And if you’ve got questions or need support, just reach out to the HazardCo team – we’re here to help.
We get it — figuring out what to do after an incident or near miss on-site can feel a bit overwhelming. One of the most common things our Advisory Team hears is, “Do I need to report this?” If it’s a notifiable event, you have a legal duty to let WorkSafe NZ know – Sounds like a lot of paperwork right? Not with HazardCo, our App makes it easy to log an incident or near miss and we’re here to guide you with what to do next!
If someone needs immediate medical treatment beyond on-site first aid, someone’s health and safety was put at serious risk, it might be classed as a notifiable event. When you report it through the App, we’ll let you know if you need to give WorkSafe a call.
Every time you report an incident or near miss, you’re helping make the site safer. It’s not about pointing fingers — it’s about learning from what happened and stopping it from happening again. Everyone on-site has the right to know about any risks, and we all play a part in keeping each other safe.
Creating a culture where everyone feels comfortable reporting issues means better communication and fewer surprises.
It’s easy:
Your report is saved in the Hub and kept on file while you’re a HazardCo member
The App will prompt you to give us a call if needed. Our Advisory Team gets a copy and will:
We recommend:
Keep records
You’re legally required to keep these records for at least 5 years. Logging everything in the App means it’s all saved in the Hub, organised and easy to access if you ever need it.
No one wants accidents to happen on site, but being prepared makes all the difference. Stay calm, follow the steps, and give us a call if you’re unsure. Our Advisory team is available 24/7 for serious incidents.
Got a question? Reach out to us today — we’re here to help.
Dust is a common hazard in the construction industry, especially during demolition or refurbishment. When buildings are demolished they can release materials that create hazardous dust (airborne contaminants) which can be hazardous to workers’ health. Understanding the risks will help you to identify how best to manage the risks.
Why is dust dangerous?
Exposure to hazardous dust can lead to serious health conditions, including:
Health and exposure monitoring
As a business, you have a duty to monitor your workers’ health when they’re exposed to dust and other hazardous materials. Regular health monitoring helps identify early signs of illness and ensures that the dust control measures in place are working effectively.
Health monitoring process should include:
It is important that you get your worker’s consent to monitor their health and engage them in this process.
Health monitoring should be carried out by a trained and competent person. For more information or if you’d like to organise health monitoring for your business contact our partner Habit Health.
How to Control dust exposure on-site
Controls to minimise the exposure to dust in the workplace could include:
Making sure your workers have the right tools and information to complete the job safely includes training and understanding the risks involved, what to do if anything should go wrong, as well as the correct use, storage, and maintenance of PPE.
Other controls to consider are:
Complete a Task Analysis for your demolition work through the HazardCo APP. This helps assess the risks and plan safe work processes. Involve your team so everyone can contribute and understand the plan.
Our team of health and safety experts are just a call away if you have any questions or would like to discuss further.
Health and safety regulators in New Zealand, are WorkSafe (the main regulator) Maritime NZ, and the Civil Aviation Authority (CAA) is here to work with you, and your workers, to keep everyone safe and healthy. Their goal is simple: to ensure that New Zealand businesses are safe and healthy places to be.
Visits to your workplace can be either pre-arranged or unannounced. Inspectors are allowed by law to show up at any reasonable time, regardless of whether or not you’re there. So, what should you expect when they come a-knocking?
Typically being inspected by WorkSafe follows a four-step process:
A friendly chat isn’t that scary, right? When the WorkSafe inspector first arrives, they’ll sit down with you and have a conversation. This discussion is a two-way street where they’ll want to learn about your business, the risks you have, and the steps you’re taking to minimise them. It’s also a great chance for you to ask any questions you may have.
If there’s nothing urgent that catches their attention, the inspector will typically focus on areas aligned with WorkSafe’s current KPI’s, as outlined in their latest strategy.
Worksafe has outlined three key areas of focus in their strategy:
Following the chat, the inspector will take a walk around your worksite to see if what they’ve heard from you matches up with what they actually see happening. The best thing that you can be during this, is curious. It may feel uncomfortable at times and that’s ok, discomfort just means that there’s space to grow. You’ll know you’re nailing it when it’s just a comfy casual coffee walk around.
If the inspector sees anything concerning during their walkabout, they will follow up with you to dig deeper, understand the root cause, and work out how it can be resolved.
When this happens, they will ask you a range of questions. To keep it simple, focus on the actual question being asked and remind yourself “respond, don’t react”. No matter what they point out, their questions will essentially boil down to these three:
It’s okay if you need clarification – Never feel like you can’t ask them to clarify a question further for you so that you can give them the most accurate answers you can. And if you don’t have an answer right away, it’s perfectly fine to say “I’ll come back to you with that”. Write the question down, involve your team, and follow up with the requested information. This shows the inspector that you have systems in place and are actively using them to ensure safety.
At this stage, the inspector might ask to see what kind of systems and processes you keep. This could include anything from your worker’s licenses or training certificates, machine maintenance logs, to incident reports. The focus will be on whether your records and systems support good health and safety practices for your worksite, workers and business.
That’s where your HazardCo records can make a big difference! Having a clear history of Risk Assessments, Task Analysis, Site Reviews and Toolbox Talks can go a long way in showing that you are proactive about workplace safety.
Outcomes:
If the inspector does find an issue, you’ll discuss together what needs to be done to address it.
The three main outcomes that may be issued by an inspector are as follows:
As mentioned earlier, you’ll know you’re on the right track when your interaction with the inspector doesn’t feel like an argument but more like a constructive discussion. The goal is to leave the conversation with a clear understanding of how your “referee” wants to call the game, while the inspector walks away knowing that your business isn’t one of the ones driving New Zealand’s harm statistics.
Using HazardCo can make this even easier—cutting your health and safety admin time in half while guiding you through the steps needed to keep your crew and business safe.
If you have any questions or need support, don’t hesitate to call us at HazardCo on 0800 555 339. We’re here to help!
The holiday season is over and now it’s time to get back into the swing of things. Coming back to work and reopening your site is just as important as shutting it down. The New Year is the perfect opportunity to refocus and set the tone for the year ahead. Coming back to work after a couple of weeks off can give some people a serious case of Mondayitis, so consider taking the following steps on the first day back:
Rather than diving straight into work, start with a kick-off toolbox talk. This is an essential step to rebrief your team on the SSSP (Site-Specific Safety Plan) and emergency procedures. Use this time to check that all workers are fit for work and mentally prepared after the break.
Perform a site review to identify any new hazards or potential risks that may have emerged during the downtime. Check that fences are still secure and containers are locked.
After a break, it’s crucial to ensure all structures and scaffolds are intact. Inspect scaffolds, check excavations, and assess other infrastructure that may have been affected by weather conditions during your time off. Ensure everything is in working order before resuming normal operations.
Before use, inspect all tools and equipment to confirm they are in good condition. It’s also vital to pre-start mobile plant to ensure it’s functioning correctly.
Consider a soft start to your operations. Allow your team the time to properly check their work areas, inspect equipment, and remind everyone that safety is the number one priority. This includes keeping in mind workers don’t overheat after spending the last couple of weeks in air conditioning, relaxing, and indulging. They may not be acclimatised to working in the heat.
As the weather heats up, so can risk on-site. Make sure that workers are provided with adequate protection from working in the heat so that they can do their work safely and comfortably. Here are some steps to help mitigate these risks:
If temperatures are dangerously high, it’s sometimes best to stop work until conditions improve. Consider shifting physical tasks to machinery for tasks such as lifting or digging, reducing the exposure to extreme heat.
Safety is a shared responsibility. Encourage your team to keep an eye on each other and to report any symptoms of heat stress. Prevention is key, but swift action can prevent more severe conditions from developing. For the early stages of heat-related illness, first aid can often be effective, but you should always seek medical assistance if in doubt, or if the person’s symptoms are severe. Symptoms to look out for are:
Be prepared this summer and make sure to keep the health, safety, and well-being of workers front of mind. Refer to the below resources for more information:
If you have any questions you can contact our Advisory Team on 0800 555 339.
The holiday season is almost upon us and we’re all eager to have a bit of a rest, recharge, and spend quality time with our families. As we wind up 2024, it’s a demanding time as we try to complete jobs before the holiday shutdown. This can make it tempting to take shortcuts, however, it can also lead to an increase in incidents, with the last two months of the year seeing a spike in workplace incidents.
Common factors can include time pressure, working in the heat, and fatigue. It’s important to keep the health, safety, and well-being of workers front of mind.
It’s necessary to start preparing for the holiday shutdown so you don’t have any interruptions during your break or come to a nasty surprise on your first day back.
Unsecured areas could be hazardous to members of the public, especially children. Children are unaware of the dangers so keeping them out and away from harm is key.
Download our Site Security Checklist for a comprehensive list.
Taking the time to prepare for the holiday shutdown period can help to make sure you get to spend uninterrupted time with your family and friends.
If you have any questions or would like to discuss your Health and Safety please give our Advisory team a call on 0800 555 339 or email info@hazardco.com.
We hope you have a safe and enjoyable break over the holiday season!
When you have an incident on-site, whether it’s a near miss, an injury, or a work-related illness, it’s important to document an incident report.
Incident reports don’t need to be time-consuming, lengthy or use fancy health and safety terms, you just need to describe what happened in your own words so you have a record of the incident. You can use the incident report to help explain what happened to others, such as your direct team on-site, contractors, other Employers, or the Main Contractor.
An incident report is the process of recording incidents on-site, such as near misses, injuries, illnesses and plant/property damage. It involves documenting all the facts (known so far) related to the incident.
Check out this blog on Managing and reporting incidents at work to learn more about what is considered an incident and why it’s both important and helpful to report incidents.
Hitting your body on an object is a very common example of an incident. For this incident report example, we will assume someone on-site has hit their body on a door frame and injured their shoulder.
Site Location
32 Dropsaw Lane, Wellington 6011
Date of Incident
2nd November 2024
People involved
Joe Hazard (injured)
Sam Small (witness)
Larry Large (witness)
Type of Incident
Damage ( equipment or property was damaged)
Security/Theft (site accessed unexpectedly or something was stolen)
Environment (Pollution or hazardous substance spill)
Near Miss (Something occurred but there was no harm caused)
✅ Injury (Someone was physically hurt)
Illness (Work-related illness)
Other (Something else happened)
Other (Something else happened)
Cause of Incident
This is where you select from the the list of causes what the main reason it happened was – In this case, it’s person vs object
Treatment received
First aid (performed on worksite)
✅ Medical Centre (Minor injury or illness)
Hospital (Major injury or illness)
Unsure (I’m not sure what treatment was given)
None (No treatment was required)
Type of injury
Select the category that best suits or select “other” to select your own, if you don’t know what type of injury happened you can also select “unknown”
Additional Information
Describe what happened – List the facts that are known so far about the incident such as :
*what job or activity was being performed at the time.
*What plant, equipment or tools were being used
*What went wrong
*What was the injury or damage (or the potential)
*What happened immediately after the incident
Joe Hazard was carrying plywood through a doorway on-site when he hit his shoulder on the door frame. Joe felt immediate pain in his left shoulder and struggled to lift his arm above shoulder height. Joe informed Sam Small (Supervisor) immediately and agreed to go to the local medical centre for further assessment
Pictures speak a thousand words so don’t forget that you can upload scene photos or relevant information in picture form at this step in the app, and if there’s something that you don’t want forgotten you can also create a task.
This is an example of a simple incident report, find out more about what good incident reporting looks like.
If you’re a HazardCo member, hit the Report an Incident button in the HazardCo App and follow the guided prompts to record the incident. Your membership includes 24/7 incident support, so if you need some extra help filling in the report, would like advice on if the incident is notifiable to the Regulator, or would just like to chat with an expert about how to communicate the incident to your team, we are here to help!
Remember, when you have an incident on-site, writing an incident report is just one action you need to take. Learn more about what to do when you have an incident on site.
Every year we see serious injuries and incidents involving vehicles near the top of the data that WorkSafe releases. Needless to say, anything with wheels and an engine should be at the forefront of your mind on-site.
From delivery trucks to excavators, if it moves, and it’s got some weight… then that means power! it’s going to cause some damage if it isn’t controlled. So always keep safety in mind!
Keep pedestrians and vehicles apart
Separate the two wherever you can with careful planning at the design and set up stages.
Minimise vehicle movements
Provide car and van parking away from the work area if possible. Also control entry points, and plan storage areas, so that vehicles don’t need to cross the site where people are.
Turning and reversing vehicles
A spotter wearing high-vis clothing should guide the driver who can’t see clearly behind their vehicle. Mirrors, reversing, warning alarms, sensors and cameras can also make all the difference.
People on-site
When untrained workers drive vehicles without authority, you’re in trouble. Always manage the training and access of drivers to your vehicles, including those visiting.
Visibility
The more the better, just make sure it stands out in the right way. From on-site lighting to aids for drivers (mirrors, CCTV cameras and reversing alarms) to hi-vis clothing for those on the ground. Find out more about the use of hi-vis clothing on-site in our blog here.
Accidents are preventable when risk is managed. How do you manage risk? You get a plan – a good one.
A traffic management plan documents and helps explain how risks will be managed. This might include details of:
Every site is different, but your plan should be monitored and reviewed regularly. It should also be adapted when there are changes to your work situation.
If you have any questions get in touch with the HazardCo team today