Working with heavy machinery and managing traffic on-site can be risky. But with the right checks and planning, we can keep everyone safe.
Daily machinery checks
Before starting work each day, make sure your equipment is ready to go:
Visual checks (before starting the machine):
- Check fluid and oil levels; look for leaks.
- Ensure tyres are free from damage and in good condition.
- Confirm safety mechanisms are in place and working.
- Make sure warning signs are visible and readable.
- Inspect attachments, clips, and pins for damage.
- Look over hydraulics for any issues.
Stationary function test (with the machine on):
- Test the horn and reversing alarm.
- Check that lights, pedals, and controls work properly.
- Move the bucket and arms to ensure they operate smoothly.
Moving function test:
- Test the steering.
- Ensure brakes are functioning correctly.
Using your manufacturer’s checklist or the HazardCo Heavy Machinery Prestart checklist can help you cover all these points.
Managing site traffic
Keeping vehicles and people safe on-site requires a solid traffic management plan. Here’s what to consider:
- Traffic direction: Plan routes for vehicles, cyclists, and pedestrians.
- Delivery areas: Set up clear zones and schedules for loading and unloading.
- Site layout: Define speed limits, traffic flow, and place barriers or fences where needed.
- Safe practices: Establish procedures for loading, unloading, turning, and reversing.
- Site restrictions: Be aware of noise levels and traffic volume.
- Unattended sites: Plan how excavations are managed when no one is around.
- Emergency procedures: Have clear steps in place for emergencies.
Discuss this plan during site inductions so everyone knows the rules and expectations.
Know your limits: Zone of influence
Heavy machinery can affect the stability of excavations if operated too close. Keep all heavy vehicles, materials, and spoil at least one meter outside the zone of influence unless specific designs support closer operations.
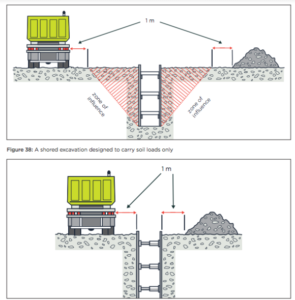
Preventing tip-overs
Uneven ground can cause machinery to tip over, leading to serious injuries. To prevent this:
- Planning: Supervisors and operators should assess the area before work begins.
- SWMS: Make sure a SWMS has been prepared.
- Risk assessment: Operators should evaluate risks before starting each job.
- Safe routes: Choose the safest paths for moving machinery.
- Digging practices: Never dig underneath an excavator.
- Distance: Work at a safe distance from excavation edges.
- Procedures: Have standard operating procedures in place.
- Design: Ensure work areas are designed to control hazards.
- Safety features: Equip cabs with roll-over and fall-over protection; operators should wear seat belts and keep doors closed.
- Exits: Ensure there are always two exits from the excavation.
If you would like more information head over to our website or to chat with one of our friendly Advisory team please give us a call on 1800 954 702.
Demolition machinery
Working with heavy machinery can be dangerous. Incorrect use or untrained operators can lead to serious injuries or worse.
Training and supervision
Machinery should only be used by workers who are:
- Trained and competent with the equipment they’re operating
- Supervised, especially if they’re new or unfamiliar with the task
- Provided with clear instructions, risk assessments and SWMS
Regularly assess operator competency through refresher training, observations and feedback. Keep training records and verify workers have the appropriate licenses.
Pre-Start Check – A quick routine that makes a big difference
Before using any machinery, complete a daily prestart check. These checks must be done by a trained and competent person.
Visual checks (before turning the machine on):
- Fluid and oil levels are good, and there are no leaks
- Battery is clean, charged and secured
- All safety guards and features are in place and undamaged
- Warning signs are in place and easy to read
- All clips, pins, and attachments are secure and not worn or damaged
- Hydraulic hoses are in good condition and lubricated
Stationary test (machine is on but not moving):
- Horn, reversing alarm and lights are working
- Pedals, and control panel are working properly
- Bucket and arms fully extend, retract and tilt smoothly
Moving test (short drive):
- Steering is responsive
- Brakes function correctly
Use the manufacturer’s pre-start checklist, or the HazardCo App Plant/Machinery Pre-start tool to guide your checks. Making sure to keep a record of your completed checks.
Quick Hitches, Safety Locks, and Exclusion Zones – Take the time to get it right
Quick hitches help you swap attachments fast – but can be dangerous if not properly secured.
Before operation:
- Confirm the attachment is the right fit and in good condition.
- Visually check all locking pins and safety devices are installed correctly.
- Set and mark exclusion zones and communicate these to all workers on-site
All quick hitches must clearly show:
- Model and serial number
- Manufacturer’s name
- Weight and max rated capacity
- Safe lifting capacity for each lifting point
Store spare locking pins with the machine, and only use attachments that match the correct pin size.
Cover any machinery risks and controls in your SWMS and share it with everyone on-site.
Don’t cut corners on safety
Missing a step like skipping a daily check or rushing an attachment change can have serious consequences.
Taking five minutes to do it right can prevent serious injuries and keep your sire running safely.
If you have any questions, get in touch with the HazardCo Team today
Digging into the ground might seem straightforward, but excavation work is actually one of the most dangerous parts of construction. That’s why it’s important to plan ahead and put the right safety measures in place to keep everyone safe on site.
Start with a solid plan
Before you get started, take some time to plan things out. Planning involves identifying the hazards, assessing the risks, and deciding suitable controls — all with input from the team. Every site is different, so take its unique features into account.
Watch out for these common excavation risks:
- Securing the area
Keep excavations fenced off with sturdy barriers that won’t give way if someone leans or falls against them. If you’re not actively working in or near the trench, cover it up or backfill it as soon as possible.
- Falls from height
If there’s a chance someone could fall from one level to another, it’s considered working at height. Make sure you have effective controls in place to prevent falls.
- Ground collapse
This is one of the biggest dangers. Don’t assume the ground will stay put. Use shoring, benching, or battering to prevent it from caving in.
- Safe ways in and out
Make sure workers have safe access at all times. Keep the bottom of the excavation clear so nothing blocks a quick exit in an emergency.
- Underground and overhead services
Always contact Before You Dig Australia. Know what’s under and above you — hidden services can be a major hazard if you hit them.
- Water in the trench
Never let workers operate in a trench that has water pooling in it unless you’ve got the right safety controls in place.
- Do you need to notify construction excavation work?
Some excavation work needs to be reported to WorkSafe Victoria before you begin. If that’s the case, you will need to notify at least three days before work starts.
Keeping yourself and your team safe is what matters most. Make sure you’re clear on your responsibilities when it comes to managing excavation risks.
Need a hand? The HazardCo App has helpful resources for site reviews and risk controls. And if you’ve got questions or need support, just reach out to the HazardCo team – we’re here to help.
When you’re able to get back on site after a flood or storm, here are the hazards, risks and control measures you should consider to help reduce the risk of injury and illness to yourself, your workers and others involved in the clean up and repair effort.
Some common hazards following a storm or flood:
- Electrical – Water damage, loss of power, damaged electrical installations
- Biological hazards and fauna – Contaminated floodwater and displaced fauna
- Asbestos – Damaged building materials that contain asbestos
- Slips, trips and falls – Uneven surfaces from storm/ floods
- Hazardous chemicals – Buried, moved or damaged hazardous chemical containers including corrosives, oils, pesticides
- Psychological stress – Remember to check on your team, the emotional impacts of a storm or flood can be overwhelming, particularly if they are dealing with personal damage
Risk Management
- Identify the hazards – What are the hazards on your site including any newly introduced hazards due to the storm or flood?
- Assess the level of risk – What is the likelihood of exposure to the hazard, and the consequences (what harm could be done)?
- Control the risk – Identify and implement suitable control measures and ensure the risk has been reduced to an acceptable level prior to undertaking related work.
- Review the control measures – Regularly assess how effective the controls are. It’s important to stop work and reassess if conditions change or if you have introduced any new hazards.
Safety tips when undertaking the cleanup and repair work
- Work out the order of the work to be done so that new risks are not introduced, e.g. if you move things in the wrong order is there a possibility of creating instability.
- Ensure surfaces are stable and access to areas with unstable floors are safe.
- Have a licensed electrical contractor check any electrical appliances or equipment you suspect has been submerged or damaged.
- Check in and under objects before attempting to move them as snakes, spiders and other undomesticated animals may be taking refuge from flood waters.
- Consider workers performing cleanup in teams/ pairs where possible.
- Wash your hands well before eating and drinking, after contact with mud, flood water and contaminated items and equipment.
- Make sure that workers have the correct personal protective equipment to prevent injuries such as cuts and scratches or infections from contaminated flood water.
- Check that your workers and contractors are not fatigued or potentially unfit to work, i.e due to mental health stressors.
- Agree on what situations workers should remove themselves from, where the risk cannot be reduced to an acceptable level. Some work may have to be delayed until water subsides and other factors.
- Ensure emergency procedures are discussed for the site with all workers.
Dust is a common hazard in the construction industry, especially during demolition or refurbishment. When buildings are demolished they can release materials that create hazardous dust (airborne contaminants) which can be hazardous to workers’ health. Understanding the risks will help you to identify how best to manage the risks.
Why is dust dangerous?
Exposure to hazardous dust can lead to serious health conditions, including:
- Silicosis – A lung disease caused by inhaling fine silica dust, common in concrete, brick, and stone materials.
- Lung Cancer – Prolonged exposure to certain airborne contaminants increases the risk.
- Asthma & COPD (Chronic Obstructive Pulmonary Disease) – Inhaling dust particles can trigger or worsen respiratory conditions.
- Skin & Eye Irritations – Dust exposure can cause infections and long-term discomfort.
Health and exposure monitoring
As a business, you have a duty to monitor your workers’ health when they’re exposed to certain substances and other hazardous materials. Regular health monitoring helps identify early signs of illness and ensures that the dust control measures in place are working effectively.
Health monitoring process should include:
- collection of workers’ demographic, medical and occupational histories
- records of workers’ exposure
- respiratory questionnaire and function tests
- in some cases, chest x-ray or other radiological procedure
It is important that you get your worker’s consent to monitor their health and engage them in this process.
Health monitoring should be carried out by a trained and competent person. They will also give recommendations based on the health monitoring results.
How to control dust exposure on-site
Controls to minimise the exposure to dust in the workplace could include:
- on-tool dust extraction systems – attach vacuum extraction directly to power tools
- water suppression – dampen materials to prevent dust from becoming airborne
- personal protective equipment (PPE) – ensure workers wear correctly fitted masks and protective gear
Making sure your workers have the right tools and information to complete the job safely includes training and understanding the risks involved, what to do if anything should go wrong, as well as the correct use, storage, and maintenance of PPE.
Other controls to consider are:
- limiting worker exposure – keep unnecessary personnel away from dusty areas
- task rotation – reduce the time any one worker spends in high-dust zones
- Dust containment – using sheeting or temporary screens to enclose the work to stop dust from escaping
Complete a SWMS for your demolition work through the HazardCo APP. This helps assess the risks and plan safe work processes. Involve your team so everyone can contribute and understand the plan.
Our team of health and safety experts are just a call away if you have any questions or would like to discuss further.
The holiday season is over and now it’s time to get back into the swing of things. Coming back to work and reopening your site is just as important as shutting it down. The New Year is the perfect opportunity to refocus and set the tone for the year ahead. Coming back to work after a couple of weeks off can give some people a serious case of Mondayitis, so consider taking the following steps on the first day back:
- Hold a kick-off Toolbox meeting to re-brief the team
Rather than diving straight into work, start with a kick-off toolbox talk. This is an essential step to rebrief your team on the SSSP (Site-Specific Safety Plan), emergency procedures, and Safe Work Method Statements (SWMS). Use this time to check that all workers are fit for work and mentally prepared after the break.
- Complete a Site Review to identify any new hazards
Perform a site review to identify any new hazards or potential risks that may have emerged during the downtime. Check that fences are still secure and containers are locked.
- Inspect Structures, Scaffolding, and Excavations
After a break, it’s crucial to ensure all structures and scaffolds are intact. Inspect scaffolds, check excavations, and assess other infrastructure that may have been affected by weather conditions during your time off. Ensure everything is in working order before resuming normal operations.
- Check Tools, Equipment, and Mobile Plant
Before use, inspect all tools and equipment to confirm they are in good condition. It’s also vital to pre-start mobile plant to ensure it’s functioning correctly.
- Start Slow: Prioritize a Safe and Smooth Transition
Consider a soft start to your operations. Allow your team the time to properly check their work areas, inspect equipment, and remind everyone that safety is the number one priority. This includes keeping in mind workers don’t overheat after spending the last couple of weeks in air conditioning, relaxing, and indulging. They may not be acclimatised to working in the heat.
- Manage the Risks of Working in Hot Conditions
As the weather heats up, so can risk on-site. Make sure that workers are provided with adequate protection from working in the heat so that they can do their work safely and comfortably. Here are some steps to help mitigate these risks:
-
-
- Provide Adequate Shade and Shelter: Set up shade tents or additional undercover areas if working outdoors. Ensure that windows are open, or fans are in use in indoor workspaces.
- Ensure Hydration and Protection from the Sun: Workers should have constant access to drinking water, sunscreen, and wear appropriate PPE like lightweight clothing, sunglasses, and sun-protective hats.
- Monitor Heat-Related Illness: Not everyone reacts to heat the same way. Be aware of the symptoms of heat-related illness such as dizziness, nausea, pale skin, rapid breathing, heat cramps, and dehydration. If a worker shows signs of heat illness, provide first aid and seek medical attention if necessary.
- Know When to Stop Work in Extreme Heat
If temperatures are dangerously high, it’s sometimes best to stop work until conditions improve. Consider shifting physical tasks to machinery for tasks such as lifting or digging, reducing the exposure to extreme heat.
- Support and Look Out for One Another
Safety is a shared responsibility. Encourage your team to keep an eye on each other and to report any symptoms of heat stress. Prevention is key, but swift action can prevent more severe conditions from developing. For the early stages of heat-related illness, first aid can often be effective, but you should always seek medical assistance if in doubt, or if the person’s symptoms are severe.
Symptoms to look out for are:
-
-
- Dizziness and feeling weak
- Vomiting and nausea
- Pale, cool and clammy skin
- Rapid breathing and shortness of breath
- Heat cramps resulting from heavy sweating without replacing salt and electrolytes
- Dehydration from increased sweating and workers not drinking enough water
Be prepared this summer and make sure to keep the health, safety, and well-being of workers front of mind. Refer to the below resources for more information:
If you have any questions you can contact our Advisory Team on 1800 954 702.
The holiday season is almost upon us, and we’re all eager to have a bit of a rest, recharge, and spend quality time with our families. As we wind up 2024, it is a demanding time for construction as we try to complete jobs before the holiday shutdown. This can make it tempting to take shortcuts, however, it can also lead to an increase in incidents, with the last two months of the year seeing a spike in workplace incidents.
Common factors can include time pressure, working in the heat, and fatigue. It’s important to keep the health, safety, and well-being of workers front of mind.
It’s necessary to start preparing for the Christmas shutdown so that you don’t have any interruptions during your break or come to a nasty surprise on your first day back. This is particularly important with residential sites which are mostly in populated areas.
Unsecured sites could be hazardous to members of the public, especially children, particularly with sites near parks, schools, homes or recreational areas. Children are unaware of the dangers of a construction site so keeping them out is key.
A safe and secure site is more than just locking the gates. Ask yourself the following questions:
- Is the worksite fenced off from the public and the boundary secure?
Make sure your site is securely fenced and all entrances are locked. Ensure your fencing is a sufficient height and that the gap at the bottom isn’t too big that people including children could squeeze through underneath.
- Is clear signage present to warn people of danger?
Make sure your Hazard Board is up to date listing the current hazards and your contact details are clearly visible in case something does pop up you can be contacted quickly. If you need to order a project for your job this can be done through the HazardCo HUB.
- Have steps been taken to prevent any unauthorised access, e.g. are all ladders removed or their rungs boarded so they can’t be used?
Remove any temptation to access hazardous areas. Where practical, remove all ladders from the site, including scaffolding and excavation ladders, or block access to these accessways.
- Are excavations and openings securely covered, fenced off, or backfilled?
Cover and fence off any excavations to prevent potential falls. Where practical backfilling excavations are recommended.
- Is all plant immobilised to prevent unauthorised use?
If you are unable to remove your vehicles or plant from the site, make sure they are left in a secure area, preferably out of sight and the keys removed.
- Are materials safely stacked and secured?
Ensure building materials are safely stacked and stored so they can’t topple or be knocked over.
- Are all flammable or dangerous substances locked away in secure storage places?
Lock up your hazardous substances in secure storage appropriate for the type of substances being stored. Where possible remove hazardous substances from the site.
- Are temporary structures stable and able to withstand bad weather conditions?
Check your temporary structures such as scaffolding and barriers to ensure they are secure and stable. Taking into consideration the changing weather.
- Has the mains power been switched off?
Make sure the builder’s temporary or main power supply and switchboard are switched off and locked out.
- Do unwanted construction materials and waste need to be removed from the site?
A quick clean-up can make a big difference. Make sure you remove all waste and empty skip bins on site.
Download our Site Security Checklist for a comprehensive list.
Some other things to consider
- Doing a Site Review on the HazardCo App on the last day before you lock up will ensure you haven’t missed anything. Completing one when you return back to site gives you the opportunity to pick any additional hazards that may have occurred while away.
- Although not recommended, if you do have lone workers on-site over the holiday season, ensure you have a lone worker policy in place. Key points are setting up regular check-ins, first aid kit on hand, a trained first aider, and to not carry out any high-risk work. See our lone worker article for more details.
- In higher risk areas you may want to consider organising security to do regular patrols.
Taking the time to prepare your site for the holiday shutdown can help to make sure you get to spend uninterrupted time with your family and friends.
If you have any questions or would like to discuss your Health and Safety please give our Advisory Team a call on 1800 954 702 or email info@hazardco.com.
We hope you have a safe and enjoyable break over the holiday season!
When you have an incident on-site, whether it’s a near miss, an injury, or a work-related illness, it’s important to document an incident report.
Incident reports don’t need to be time-consuming, lengthy or use fancy health and safety terms, you just need to describe what happened in your own words so you have a record of the incident. You can use the incident report to help explain what happened to others, such as your direct team on-site, contractors, other Employers, or the Principal Contractor.
What is an incident report?
An incident report is the process of recording incidents on-site, such as near misses, injuries, illnesses and plant/property damage. It involves documenting all the facts (known so far) related to the incident.
Check out this blog on managing and reporting incidents at work to learn more about what is considered an incident and why it’s both important and helpful to report incidents.
How to complete an incident report
Example incident report: Hit body on object
Hitting your body on an object is a very common example of an incident. For this incident report example, we will assume someone on-site has hit their body on a door frame and injured their shoulder.
- Site Location
- 32 Dropsaw Lane, Cottesloe 6011
- People involved
- Joe Hazard (injured)
- Sam Small (witness)
- Larry Large (witness)
- Type of Incident
- Damage (equipment or property was damaged)
- Security/Theft (site accessed unexpectedly or something was stolen)
- Environment (Pollution or hazardous substance spill)
- Near Miss (Something occurred but there was no harm caused)
- Injury (Someone was physically hurt) ✅
- Illness (Work-related illness)
- Other (Something else happened)
- Other (Something else happened)
- Cause of Incident
- This is where you select from the the list of causes what the main reason for it occurring was – in this case, it’s person vs object.
- Treatment received
- First aid (performed on worksite)
- Medical Centre (Minor injury or illness) ✅
- Hospital (Major injury or illness)
- Unsure (I’m not sure what treatment was given)
- None (No treatment was required)
- Type of injury
- Select the category that best suits or select “other” to select your own, if you don’t know what type of injury happened you can also select “unknown”.
- Describe what happened – List the facts that are known so far about the incident such as :
- What job or activity was being performed at the time.
- What plant, equipment or tools were being used
- What went wrong
- What was the injury or damage (or the potential)
- What happened immediately after the incident
-
- Joe Hazard was carrying plywood through a doorway on-site when he hit his shoulder on the door frame. Joe felt immediate pain in his left shoulder and struggled to lift his arm above shoulder height. Joe informed Sam Small (Supervisor) immediately and agreed to go to the local medical centre for further assessment.
Pictures speak a thousand words so don’t forget that you can upload scene photos or relevant information in picture form at this step in the app, and if there’s something that you don’t want forgotten you can also create a task.
This is an example of a simple incident report, find out more about what good incident reporting looks like.
If you’re a HazardCo member, hit the Report an Incident button in the HazardCo App and follow the guided prompts to record the incident. Your membership includes 24/7 incident support, so if you need some extra help filling in the report, would like advice on if the incident is notifiable to the Regulator, or would just like to chat with an expert about how to communicate the incident to your team, we are here to help!
Remember, when you have an incident on-site, writing an incident report is just one action you need to take. Learn more about what to do when you have an incident on site.
Anything with wheels and an engine should be at the forefront of your mind on site.
From delivery trucks to excavators, if it moves, and it’s got some weight… then that means power! it’s going to cause some damage if it isn’t controlled. So always keep safety in mind!
Keep pedestrians and vehicles apart
Separate the two wherever you can with careful planning at the design and set up stages.
Minimise vehicle movements
Provide car and van parking away from the work area if possible. Also control entry points, and plan storage areas, so that vehicles don’t need to cross the site where people are.
Turning and reversing vehicles
A spotter wearing high-vis clothing should guide the driver who can’t see clearly behind their vehicle. Mirrors, reversing, warning alarms, sensors and cameras can also make all the difference.
People on-site
When untrained workers drive vehicles without authority, you’re in trouble. Always manage the training and access of drivers to your vehicles, including those visiting.
Visibility
The more the better, just make sure it stands out in the right way. From on-site lighting to aids for drivers (mirrors, CCTV cameras and reversing alarms) to hi-vis clothing for those on the ground. Find out more about the use of hi-vis clothing on-site in our blog here.
Accidents are preventable when risk is managed. How do you manage risk? You get a plan – a good one.
Traffic management plans
A traffic management plan documents and helps explain how risks will be managed. This might include details of:
- Designated travel paths for vehicles including entry and exit points
- Pedestrian and traffic routes
- Designated delivery and loading/unloading areas
- Travel paths on routes remote from the workplace, including places to turn around, dump material, access ramps and side roads
- The responsibilities of people expected to interact with traffic onsite
Every site is different, but your plan should be monitored and reviewed regularly. It should also be adapted when there are changes to your work situation.
If you have any questions get in touch with the HazardCo team today
Electricity is essential on construction sites, but if the risks are not managed properly, it can pose serious dangers to people and property. Proper controls must be in place wherever electricity is used to keep everyone safe.
Because we use electricity differently across a site there are different ways to help manage the risks.
Residual Current Devices (RCDs)
An RCD is an electrical safety device designed to immediately switch off the supply of electricity when electricity ‘leaking’ to earth is detected at harmful levels. RCDs offer high levels of personal protection from electric shock.
There are three types of RCD:
Fixed at the switchboard
- A switchboard RCD is the best option in most situations. It protects all the electrical wiring and appliances supplied from that circuit.
- An electrician must install a switchboard RCD.
Built into the powerpoint
- A socket-outlet RCD is built into a standard powerpoint to provide protection to equipment plugged into that powerpoint and, if required, downstream protection of other powerpoints.
- An electrician must install a socket-outlet RCD.
Portable
- A portable RCD can be moved from powerpoint to powerpoint as needed. There are a few different types of portable RCD:
- Some plug directly into a powerpoint. An appliance or extension lead then plugs into the portable RCD.
- Some are built into extension leads or individual appliance leads.
- Some are built into Portable socket-outlet assemblies (PSOAs).
- No electrician is needed – you can buy a portable RCD at a hardware shop or from an electrical equipment supplier, just make sure it is fit for purpose.
Testing
Keep you and your team safe while working around electricity by checking your RCD regularly. Across Australia, the testing frequency is based off the standard, AS/NZS 3012:2019 which sets the specific requirements for construction sites and states:
- Portable RCDs are to be push button tested daily before every use and an operating time test is to be performed by a competent person every 3 months.
- Fixed RCDs are to be push button tested 1 month and an operating time test is to be performed by a competent person every 12 months.
If an RCD is tested and found to be faulty it must be taken out of service immediately and replaced as soon as possible.
Leads and Cords
Leads and cords are easily damaged, particularly those connected to equipment that is often moved. To protect them:
- Use cable protectors, covers, non-conductive hooks, and ramps.
- Protect leads from sharp objects, footwear, doors, vehicles, liquids, grease, and heat.
- Arrange leads to prevent tripping hazards. Avoid running leads across aisles or passages.
- Elevate leads to keep them off the ground and ensure they are accessible without needing a ladder.
- Use insulated supports to relieve strain on plugs.
- Inspect leads for damage before use and have them tested and tagged regularly by a qualified person.
Testing and Tagging of leads and cords
Inspection, testing and tagging of electrical leads and cords on construction sites are required to be completed every 3 months* by a competent person.
Any lead or cord that is damaged or that fails testing is to be immediately taken out of use and removed offsite. If you cannot promptly remove it offsite, consider other means like attaching a durable out of service tag so as to warn workers not to use that piece of equipment.
Monitor and Review
When you complete your regular Site Reviews using the HazardCo App, make sure that you are checking RCD’s and all other electrical equipment are in good working condition and are regularly inspected and tested.
Further Information
If you have any questions in regards to this topic or need more support , reach out to HazardCo and speak to one of our expert Health and Safety Advisors. You can contact us on 1800 954 702.
*For Hire equipment, inspection is required prior to each hire and testing is carried out at least monthly. If hire equipment remains on the construction site then the frequency listed applies.
Looking for something in particular?
Working with heavy machinery and managing traffic on-site can be risky. But with the right checks and planning, we can keep everyone safe.
Daily machinery checks
Before starting work each da...
Demolition machinery
Working with heavy machinery can be dangerous. Incorrect use or untrained operators can lead to serious injuries or worse.
Training and supervision
Machinery sho...
Digging into the ground might seem straightforward, but excavation work is actually one of the most dangerous parts of construction. That’s why it’s important to plan ahead and put the right s...
When you're able to get back on site after a flood or storm, here are the hazards, risks and control measures you should consider to help reduce the risk of injury and illness to yourself, you...
Dust is a common hazard in the construction industry, especially during demolition or refurbishment. When buildings are demolished they can release materials that create hazardous dust (airbor...
The holiday season is over and now it’s time to get back into the swing of things. Coming back to work and reopening your site is just as important as shutting it down. The New Year is the per...
The holiday season is almost upon us, and we’re all eager to have a bit of a rest, recharge, and spend quality time with our families. As we wind up 2024, it is a demanding time for constructi...
When you have an incident on-site, whether it’s a near miss, an injury, or a work-related illness, it’s important to document an incident report.
Incident reports don’t need to be time-cons...
Anything with wheels and an engine should be at the forefront of your mind on site.
From delivery trucks to excavators, if it moves, and it’s got some weight… then that means power! it’s g...
Electricity is essential on construction sites, but if the risks are not managed properly, it can pose serious dangers to people and property. Proper controls must be in place wherever electri...
Health and safety is a core part of any business but incidents and injuries on the job can still happen. According to SafeWork Australia, in the construction industry alone there were 15,877 s...
The HazardCo App has a new Plant/Machinery Pre-Start tool! It’s a quick and easy way to do pre-start checks on various plant and machinery such as scissor lists, boom lifts and excavators. Jus...