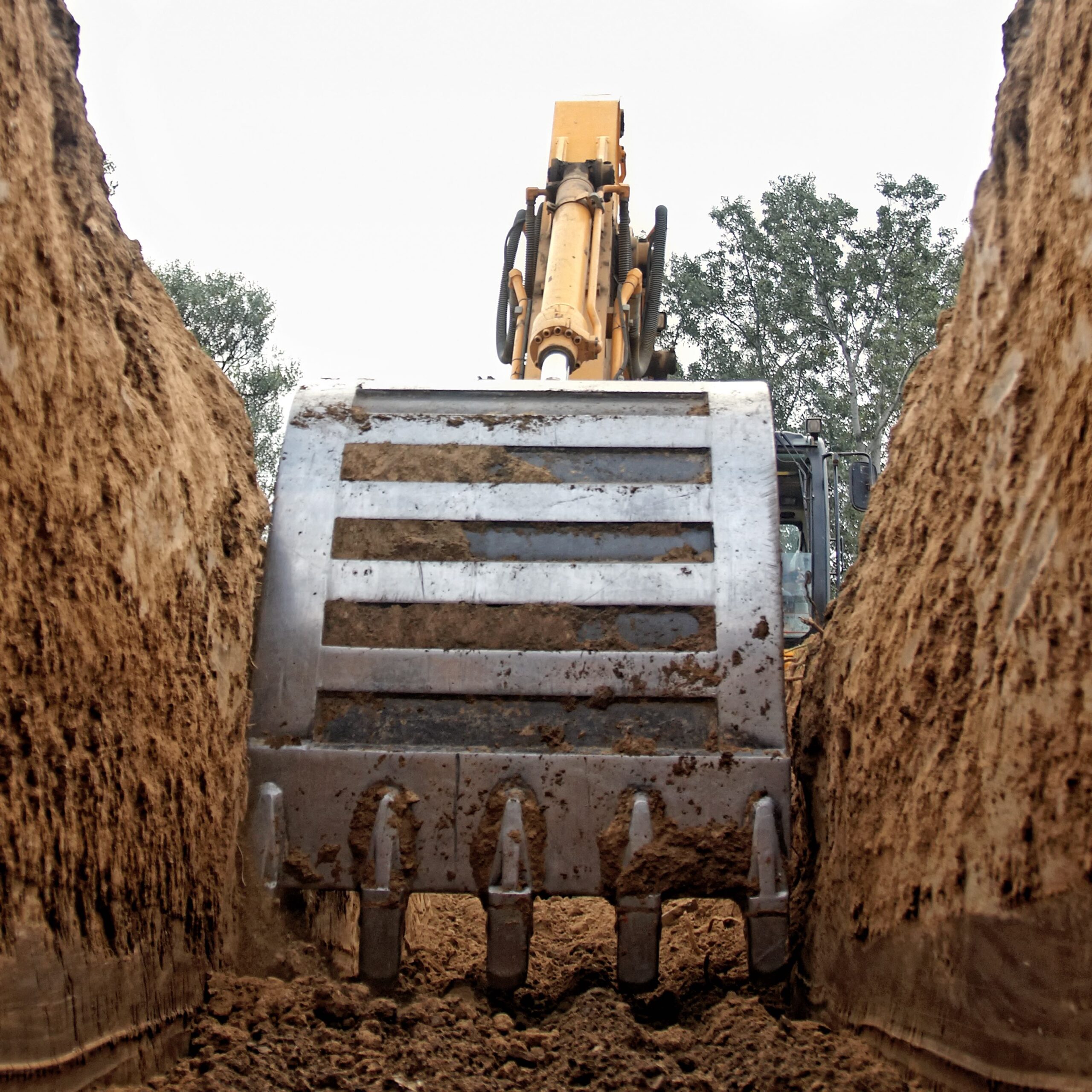
Working with heavy machinery and managing traffic on-site can be risky. But with the right checks and planning, we can keep everyone safe.
Before starting work each day, make sure your equipment is ready to go:
Visual checks (before starting the machine):
Stationary function test (with the machine on):
Moving function test:
Using your manufacturer’s checklist or the HazardCo Heavy Machinery Prestart checklist can help you cover all these points.
Keeping vehicles and people safe on-site requires a solid traffic management plan. Here’s what to consider:
Discuss this plan during site inductions so everyone knows the rules and expectations.
Heavy machinery can affect the stability of excavations if operated too close. Keep all heavy vehicles, materials, and spoil at least one meter outside the zone of influence unless specific designs support closer operations.
Uneven ground can cause machinery to tip over, leading to serious injuries. To prevent this:
If you would like more information head over to our website or to chat with one of our friendly Advisory team please give us a call on 0800 555 339.
Operating Machinery
Working with heavy machinery can be dangerous. Incorrect use or untrained operators can lead to serious injuries or worse.
Training and Supervision
Machinery should only be used by workers who are:
Regularly assess operator competency through refresher training, observations and feedback. Keep training records and verify workers have the appropriate licenses.
Before using any machinery, complete a daily prestart check. These checks must be done by a trained and competent person.
Visual checks (before turning the machine on):
Stationary test (machine is on but not moving):
Moving test (short drive):
Use the manufacturer’s pre-start checklist, the HazardCo Heavy Machinery Prestart Checklist or the HazardCo App Plant/Machinery Pre-start tool to guide your checks. Making sure to keep a record of your completed checks.
Quick Hitches, Safety Locks, and Exclusion Zones – Take the time to get it right
Quick hitches help you swap attachments fast – but can be dangerous if not properly secured.
Before operation:
All quick hitches must clearly show:
Store spare locking pins with the machine, and only use attachments that match the correct pin size.
Cover any machinery risks and controls in your task analysis and share it with everyone on-site.
Don’t cut corners on safety
Missing a step like skipping a daily check or rushing an attachment change can have serious consequences.
Taking five minutes to do it right can prevent serious injuries and keep your sire running safely.
If you have any questions, get in touch with the HazardCo Team today
Digging into the ground might seem straightforward, but excavation work is actually one of the most dangerous parts of construction. That’s why it’s important to plan ahead and put the right safety measures in place to keep everyone safe on site.
Before you get started, take time to plan things out. Planning means identifying the hazards, assessing the risks, and deciding suitable controls – with input from the team. Make sure an emergency plan is in place in case something goes wrong. Every site is different, so take its unique features into account when planning.
Keeping yourself and your team safe is what matters most. Make sure you’re clear on your responsibilities when it comes to managing excavation risks.
Need a hand? The HazardCo App has helpful resources for site reviews and risk controls. And if you’ve got questions or need support, just reach out to the HazardCo team – we’re here to help.
Dust is a common hazard in the construction industry, especially during demolition or refurbishment. When buildings are demolished they can release materials that create hazardous dust (airborne contaminants) which can be hazardous to workers’ health. Understanding the risks will help you to identify how best to manage the risks.
Why is dust dangerous?
Exposure to hazardous dust can lead to serious health conditions, including:
Health and exposure monitoring
As a business, you have a duty to monitor your workers’ health when they’re exposed to dust and other hazardous materials. Regular health monitoring helps identify early signs of illness and ensures that the dust control measures in place are working effectively.
Health monitoring process should include:
It is important that you get your worker’s consent to monitor their health and engage them in this process.
Health monitoring should be carried out by a trained and competent person. For more information or if you’d like to organise health monitoring for your business contact our partner Habit Health.
How to Control dust exposure on-site
Controls to minimise the exposure to dust in the workplace could include:
Making sure your workers have the right tools and information to complete the job safely includes training and understanding the risks involved, what to do if anything should go wrong, as well as the correct use, storage, and maintenance of PPE.
Other controls to consider are:
Complete a Task Analysis for your demolition work through the HazardCo APP. This helps assess the risks and plan safe work processes. Involve your team so everyone can contribute and understand the plan.
Our team of health and safety experts are just a call away if you have any questions or would like to discuss further.
The holiday season is over and now it’s time to get back into the swing of things. Coming back to work and reopening your site is just as important as shutting it down. The New Year is the perfect opportunity to refocus and set the tone for the year ahead. Coming back to work after a couple of weeks off can give some people a serious case of Mondayitis, so consider taking the following steps on the first day back:
Rather than diving straight into work, start with a kick-off toolbox talk. This is an essential step to rebrief your team on the SSSP (Site-Specific Safety Plan) and emergency procedures. Use this time to check that all workers are fit for work and mentally prepared after the break.
Perform a site review to identify any new hazards or potential risks that may have emerged during the downtime. Check that fences are still secure and containers are locked.
After a break, it’s crucial to ensure all structures and scaffolds are intact. Inspect scaffolds, check excavations, and assess other infrastructure that may have been affected by weather conditions during your time off. Ensure everything is in working order before resuming normal operations.
Before use, inspect all tools and equipment to confirm they are in good condition. It’s also vital to pre-start mobile plant to ensure it’s functioning correctly.
Consider a soft start to your operations. Allow your team the time to properly check their work areas, inspect equipment, and remind everyone that safety is the number one priority. This includes keeping in mind workers don’t overheat after spending the last couple of weeks in air conditioning, relaxing, and indulging. They may not be acclimatised to working in the heat.
As the weather heats up, so can risk on-site. Make sure that workers are provided with adequate protection from working in the heat so that they can do their work safely and comfortably. Here are some steps to help mitigate these risks:
If temperatures are dangerously high, it’s sometimes best to stop work until conditions improve. Consider shifting physical tasks to machinery for tasks such as lifting or digging, reducing the exposure to extreme heat.
Safety is a shared responsibility. Encourage your team to keep an eye on each other and to report any symptoms of heat stress. Prevention is key, but swift action can prevent more severe conditions from developing. For the early stages of heat-related illness, first aid can often be effective, but you should always seek medical assistance if in doubt, or if the person’s symptoms are severe. Symptoms to look out for are:
Be prepared this summer and make sure to keep the health, safety, and well-being of workers front of mind. Refer to the below resources for more information:
If you have any questions you can contact our Advisory Team on 0800 555 339.
The holiday season is almost upon us and we’re all eager to have a bit of a rest, recharge, and spend quality time with our families. As we wind up 2024, it’s a demanding time as we try to complete jobs before the holiday shutdown. This can make it tempting to take shortcuts, however, it can also lead to an increase in incidents, with the last two months of the year seeing a spike in workplace incidents.
Common factors can include time pressure, working in the heat, and fatigue. It’s important to keep the health, safety, and well-being of workers front of mind.
It’s necessary to start preparing for the holiday shutdown so you don’t have any interruptions during your break or come to a nasty surprise on your first day back.
Unsecured areas could be hazardous to members of the public, especially children. Children are unaware of the dangers so keeping them out and away from harm is key.
Download our Site Security Checklist for a comprehensive list.
Taking the time to prepare for the holiday shutdown period can help to make sure you get to spend uninterrupted time with your family and friends.
If you have any questions or would like to discuss your Health and Safety please give our Advisory team a call on 0800 555 339 or email info@hazardco.com.
We hope you have a safe and enjoyable break over the holiday season!
When you have an incident on-site, whether it’s a near miss, an injury, or a work-related illness, it’s important to document an incident report.
Incident reports don’t need to be time-consuming, lengthy or use fancy health and safety terms, you just need to describe what happened in your own words so you have a record of the incident. You can use the incident report to help explain what happened to others, such as your direct team on-site, contractors, other Employers, or the Main Contractor.
An incident report is the process of recording incidents on-site, such as near misses, injuries, illnesses and plant/property damage. It involves documenting all the facts (known so far) related to the incident.
Check out this blog on Managing and reporting incidents at work to learn more about what is considered an incident and why it’s both important and helpful to report incidents.
Hitting your body on an object is a very common example of an incident. For this incident report example, we will assume someone on-site has hit their body on a door frame and injured their shoulder.
Site Location
32 Dropsaw Lane, Wellington 6011
Date of Incident
2nd November 2024
People involved
Joe Hazard (injured)
Sam Small (witness)
Larry Large (witness)
Type of Incident
Damage ( equipment or property was damaged)
Security/Theft (site accessed unexpectedly or something was stolen)
Environment (Pollution or hazardous substance spill)
Near Miss (Something occurred but there was no harm caused)
✅ Injury (Someone was physically hurt)
Illness (Work-related illness)
Other (Something else happened)
Other (Something else happened)
Cause of Incident
This is where you select from the the list of causes what the main reason it happened was – In this case, it’s person vs object
Treatment received
First aid (performed on worksite)
✅ Medical Centre (Minor injury or illness)
Hospital (Major injury or illness)
Unsure (I’m not sure what treatment was given)
None (No treatment was required)
Type of injury
Select the category that best suits or select “other” to select your own, if you don’t know what type of injury happened you can also select “unknown”
Additional Information
Describe what happened – List the facts that are known so far about the incident such as :
*what job or activity was being performed at the time.
*What plant, equipment or tools were being used
*What went wrong
*What was the injury or damage (or the potential)
*What happened immediately after the incident
Joe Hazard was carrying plywood through a doorway on-site when he hit his shoulder on the door frame. Joe felt immediate pain in his left shoulder and struggled to lift his arm above shoulder height. Joe informed Sam Small (Supervisor) immediately and agreed to go to the local medical centre for further assessment
Pictures speak a thousand words so don’t forget that you can upload scene photos or relevant information in picture form at this step in the app, and if there’s something that you don’t want forgotten you can also create a task.
This is an example of a simple incident report, find out more about what good incident reporting looks like.
If you’re a HazardCo member, hit the Report an Incident button in the HazardCo App and follow the guided prompts to record the incident. Your membership includes 24/7 incident support, so if you need some extra help filling in the report, would like advice on if the incident is notifiable to the Regulator, or would just like to chat with an expert about how to communicate the incident to your team, we are here to help!
Remember, when you have an incident on-site, writing an incident report is just one action you need to take. Learn more about what to do when you have an incident on site.
Every year we see serious injuries and incidents involving vehicles near the top of the data that WorkSafe releases. Needless to say, anything with wheels and an engine should be at the forefront of your mind on-site.
From delivery trucks to excavators, if it moves, and it’s got some weight… then that means power! it’s going to cause some damage if it isn’t controlled. So always keep safety in mind!
Keep pedestrians and vehicles apart
Separate the two wherever you can with careful planning at the design and set up stages.
Minimise vehicle movements
Provide car and van parking away from the work area if possible. Also control entry points, and plan storage areas, so that vehicles don’t need to cross the site where people are.
Turning and reversing vehicles
A spotter wearing high-vis clothing should guide the driver who can’t see clearly behind their vehicle. Mirrors, reversing, warning alarms, sensors and cameras can also make all the difference.
People on-site
When untrained workers drive vehicles without authority, you’re in trouble. Always manage the training and access of drivers to your vehicles, including those visiting.
Visibility
The more the better, just make sure it stands out in the right way. From on-site lighting to aids for drivers (mirrors, CCTV cameras and reversing alarms) to hi-vis clothing for those on the ground. Find out more about the use of hi-vis clothing on-site in our blog here.
Accidents are preventable when risk is managed. How do you manage risk? You get a plan – a good one.
A traffic management plan documents and helps explain how risks will be managed. This might include details of:
Every site is different, but your plan should be monitored and reviewed regularly. It should also be adapted when there are changes to your work situation.
If you have any questions get in touch with the HazardCo team today
Emergencies and natural disasters can happen any time. Although you can’t predict when they will happen, you can take actions to make your business more prepared.
Do you and your workers know what to do if a disaster strikes?
An emergency plan is a health and safety requirement necessary for keeping everyone safe, and not having one is a big risk for your business and your workers.
Your emergency plan should include the following:
What to consider when making an emergency plan:
When working out your emergency plan, you must take into account:
Maintaining and testing emergency plans:
A well-maintained emergency plan should be reviewed and updated when:
Testing your emergency plan is important to ensure it works:
Worker Engagement
Involve workers in emergency planning and decisions. All workers should know who is responsible for activating and coordinating emergency procedures and what they must do to keep themselves and others safe in an emergency.
First Aid Kits and Fire Extinguishers
Having first aid kits and fire extinguishers readily available ensures that workers can quickly address emergencies, potentially saving lives and preventing extensive property damage.
Sort your safety with an Emergency Box for your work vehicle or fixed to your wall at your site! Our Emergency Boxes are designed to provide the essentials for an emergency situation in all types of workplaces.
Not only will they help to keep health and safety front and centre but having a first aid kit, fire extinguisher, air horn, and emergency plan right at your fingertips will keep you covered in case of any unexpected incidents.
To order, call us on 0800 555 339 or email info@hazardco.com.
Keeping you and your workmates safe at work is a top priority, so it’s important to understand what your business needs for an effective emergency plan. Make sure you’re aware of these requirements to help keep everyone safe!
If you would like more information, get in touch with our friendly HazardCo team – we’re always happy to help!
Electricity is essential on construction sites, but if the risks are not managed properly, it can pose serious dangers to people and property. Proper controls must be in place wherever electricity is used to keep everyone safe.
Because we use electricity differently across a site there are different ways to help manage the risks.
All hand-held appliances, lights, and electrical equipment used on-site must have protection in place against electric shock This can be done simply by connecting all electrical equipment through an RCD.
An RCD continuously monitors the electric current flowing along a circuit and disconnects the electricity supply if a fault is detected, reducing the risk of electric shock.
Fixed at the switchboard
A switchboard RCD is the most effective option. It protects all the wiring and appliances on that circuit. This must be installed by a licensed electrician.
Built into the powerpoint
A socket-outlet RCD is built into a standard powerpoint and protects equipment plugged into it. A licensed electrician is required for installation.
Portable
A portable RCD can be moved between powerpoints as needed. There are a few different types of portable RCD:
No electrician is needed – you can buy a portable RCD at a hardware shop or electrical equipment supplier, just make sure they are fit for commercial use. Both portable and non-portable RCDs should be tested daily.
Keep you and your team safe while working around electricity by checking your RCD (using the test button) daily before use. Get RCDs tested by a trained and competent person regularly, at least every three months.
Leads and cords are easily damaged, particularly those connected to equipment that is often moved. To protect them:
Check out our one-pager on Electrical Safety. You can print and display this at work, helping everyone manage electrical shock risks on-site.
During regular Site Reviews using the HazardCo App, check that RCDs and all electrical equipment are in good condition and have been tested and tagged. Electrical equipment should be tested and tagged every 3 months for construction, every 6 months for manufacturing, and every 12 months for low-use spaces such as offices.
For any questions or support, contact HazardCo and speak to one of our Health and Safety Advisors on 0800 555 339.