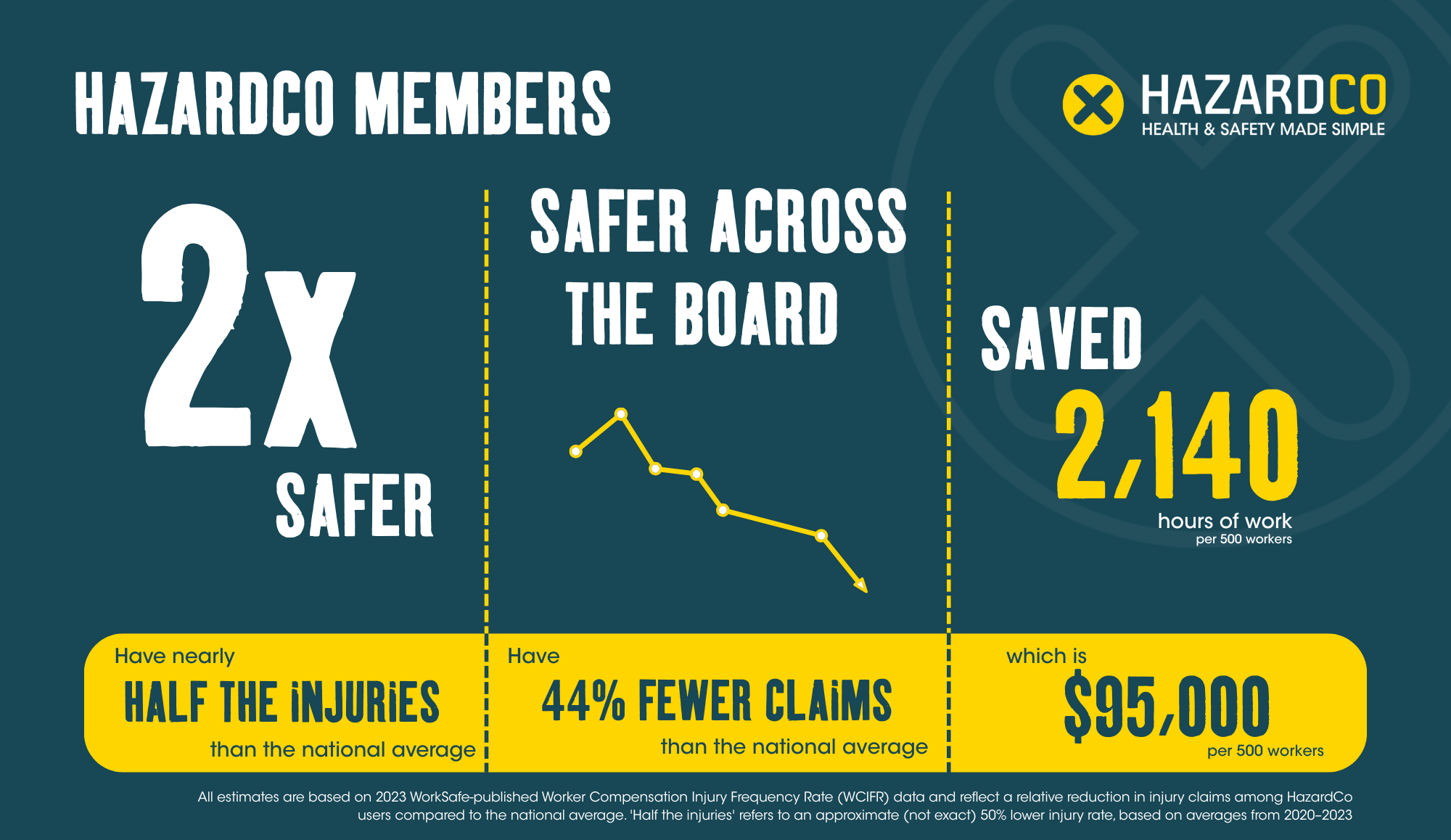
At HazardCo, we’re all about making health and safety simple – and it’s working. New data shows that our members are safer on site compared to the national average. Whether you’re on the tools or managing a team, these numbers show the real impact of doing health and safety the HazardCo way.
There’s a big difference between having a health and safety system and using one that actually works.
At HazardCo, we don’t just help you tick boxes. Our guided tools make it easy to follow the right health and safety steps at the right time — and when that happens, sites are safer. Now we’ve got the data to back it up.
New stats show that HazardCo members are significantly safer on site than the national average. Whether you’re on the tools or running the business, this proves that doing health and safety the HazardCo way pays off.
We’ve crunched the numbers and here’s what we found:
That’s a massive difference.
Why it’s working
Our digital tools make it easy to manage health and safety day to day. From guided Site Reviews that help you put the right controls in place, to risk assessments, toolbox talks, site inductions, SWMS and incident reports — it’s all handled in the HazardCo App.
Everyone on site can get involved, making it easier to spot risks early, take action, and keep things running smoothly. Plus, if something does go sideways, our expert advisors are available 24/7 to help you respond the right way.
When health and safety is easy to follow and part of your everyday routine, it becomes second nature – and it keeps people safer.
Fewer injuries mean less time off the tools, and that saves your business money. When your team stays safe, you avoid costly downtime, keep your jobs on track, and reduce the chance of needing to bring in extra workers to cover.
You’ll also be in a better position if the Regulator (Worksafe / Safework) ever comes knocking. HazardCo helps you meet your legal responsibilities and show you’re doing things properly, without the paperwork pile-up.
A well-run site is a safer site. It’s better for your crew, your schedule, and your bottom line.
Using HazardCo isn’t just about ticking boxes faster, it’s about making your site genuinely safer.
You’re working smarter, with fewer accidents, less downtime, and more time getting the job done right.
Our mission is to keep the person at the top of the ladder safe, and the data shows it’s working.
Not a member yet? Maybe it’s time to make the switch.
Over the next 5 years Australia’s multi-dwelling construction industry is expected to grow due to urbanisation and strong population growth. Despite having a downturn in recent years, the number of businesses in the industry has grown 1.9% per year, reaching 27,700 in 2024.
What is Multi-Dwelling Housing?
In Australia, “multi-dwelling housing” refers to residential developments with three or more dwellings on a single lot, each with ground-level access, and excludes apartment buildings.
What’s the difference?
The key difference between single and multi-dwelling housing is the level of complexity required to manage the build and the likelihood of additional layers of responsibility e.g. directors and development owners above the principal contractor.
There are often complex stages of these builds, which are generally run by specialised subbies e.g. planning (engineers, architects, quantity surveyors), and build stages (civil works, construction management, carpentry/joiners, concreting) etc. In addition, there are often more intricate designs, additional fire safety regulation and stricter compliance standards.
Multiple dwellings also mean more trades are on-site working in close proximity to each other, and on top of that sites are located in more established areas where there is more interaction with existing residents and the general public.
Multi-dwelling Project Requirements
Because multi-dwelling housing creates more risk on-site due to the increased amount of subbies, machinery, equipment, and high-risk work taking place, It’s important that you have the right H&S tools in place for your contractors and a safe system of work e.g. Site Specific Safety Plan (SSSP) for all multi-dwelling projects.
A SSSP for a multi-dwelling build will outline how all involved parties will manage health and safety on-site. This includes details between parties on how they will manage workers, their expectations, roles, and responsibilities to ensure that all relevant site safety information is available.
Due to the potential complexity of multi-dwelling builds, we always recommend a more detailed and customised SSSP to manage risks effectively and reduce overall risk to the business and the workers.
The extra complexities that can need extra planning and control include:
Got a new multi-dwelling build kicking off?
Project Pro and the HazardCo system are suitable and capable of meeting the H&S requirements of multi-dwelling builds, so you can feel confident that HazardCo can support you as your business grows.
If you are a builder starting to diversify, now’s the right time to review your Health and Safety activity.
That’s where HazardCo comes in. If you’re building 3 or more dwellings within a fenced-off section, you will need HazardCo’s Project Pro. This is a customised project, specifically for your build that gives you everything you need for your team and all the subcontractors you will have coming onto the site.
Here are some key components of Project Pro that will help you cover all your bases.
If you have a new multi-dwelling residential project kicking off, give us a call on 1800 954 702 or email info@hazardco.com to discuss your requirements and what you need to be thinking about from a H&S perspective and the added complexities that come with it.
Managing safety on-site is no small task, especially when high-risk construction work is involved. Whether you’re working at heights, operating heavy machinery, or managing airborne contaminants, having a clear plan in place to identify and control hazards is essential.
That’s where HazardCo’s SWMS with Risk Matrix comes in.
This new feature goes beyond the basics of a standard Safe Work Method Statement (SWMS), giving you clearer documentation and stronger risk management. With a built-in Risk Matrix, you can better assess the likelihood and impact of potential hazards and demonstrate exactly how you’re reducing risk on-site.
What’s New
With SWMS Risk Matrix, you now have access to a built-in Risk Matrix that helps you make more informed, structured decisions. A risk matrix enables you to evaluate hazards based on two key factors:
By visually mapping out risks before and after control measures are applied, the risk matrix helps you plan more effectively, communicate more clearly, and maintain stronger safety records.
A risk matrix is often required when pre-qualifying or tendering for government or large-scale projects, where robust and detailed safety documentation is expected by the Principal Contractor and Clients.
But that’s not the only time it comes in handy.
A Risk Matrix is also useful in day-to-day operations, for example:
They help you reassess risks, update control measures, and engage your team in actively identifying and managing site-specific hazards.
Using a Risk Matrix provides clear evidence that hazards have been properly assessed and managed, making your SWMS easier to understand and more effective for everyone involved.
It allows you to:
Here’s why SWMS with Risk Matrix is a valuable addition to your safety toolkit:
SWMS with Risk Matrix is available on our Premium and Complete subscription plans.
If your jobs involve high-risk construction work, complex planning, or requires you to submit detailed documentation for tenders or prequalification, this tool is made for you
We get it — figuring out what to do after an incident or near miss on-site can feel a bit overwhelming. One of the most common things our Advisory Team hears is, “Do I need to report this?”If it’s a notifiable incident, you have a legal duty to let your State Regulator know – Sounds like a lot of paperwork right? Not with HazardCo, our App makes it easy to log an incident or near miss and we’re here to guide you with what to do next!
If someone needs immediate medical treatment for a serious injury, someone’s health and safety was put at serious risk, it might be classed as a notifiable incident. When you report it through the App, we’ll let you know if you need to report it.
Every time you report an incident or near miss, you’re helping make the site safer. It’s not about pointing fingers — it’s about learning from what happened and stopping it from happening again. Everyone on-site has the right to know about any risks, and we all play a part in keeping each other safe.
Creating a culture where everyone feels comfortable reporting issues means better communication and fewer surprises.
It’s easy:
Your report is saved in the Hub and kept on file while you’re a HazardCo member
What happens next?
The App will prompt you to give us a call if needed. Our Advisory Team gets a copy and will:
We recommend:
Keep records
You’re legally required to keep these records for at least 5 years. Logging everything in the App means it’s all saved in the Hub, organised and easy to access if you ever need it.
No one wants accidents to happen on site, but being prepared makes all the difference. Stay calm, follow the steps, and give us a call if you’re unsure. Our Advisory team is available 24/7 for serious incidents.
Got a question? Reach out to us today — we’re here to help.
Hand and finger injuries are one of the most common injuries on-site. Over the last year, HazardCo has received 4599 incident reports – 720 of those were hand or finger injuries. That highlights just how often these injuries happen, so let’s look at how they happen and what we can do to prevent them.
There are plenty of ways hands and fingers can get hurt on-site, but the most common injuries include:
These injuries happen due to faulty equipment, falling objects, getting caught between materials, electrical issues, and simple mistakes.
Many hand and finger injuries occur from everyday tools such as hammers, planes and utility knives, and handling metal sheets. There have also been an increasing number of injuries from nail guns. These injuries are often caused by rushing, fatigue, complacency, using damaged tools, or not having the right training.
Hand injuries aren’t just painful – they affect your ability to work and go about your daily life. Even minor injuries can weaken grip strength and finger movement. More serious injuries could mean permanent damage or loss of function.
Keeping hands safe is all about awareness and good habits. Here’s how you and your team can reduce the risk:
Safety isn’t just about following the rules. It’s about actions and leading by example. Leaders set the tone by demonstrating safe practices, sharing real stories of how hand injuries can impact lives and actively monitoring worksite conditions. Once workers understand the risk, it’s their responsibility to stay aware, but team leaders must make sure safety measures are in place and consistently followed.
Let’s work together to bring those hand injury numbers down!
Got a question about hand safety or any other health and safety issue? The HazardCo Advisory Team is here to help – call 1800 945 702
Good health and safety processes and systems lay the foundation for success with any project but are even more important with bigger builds and multi-dwelling residential projects.
This blog will dive into managing health and safety in complex construction projects and look at how to set up effective systems to lay a solid foundation for your next big project.
At HazardCo, we keep a close eye on industry trends to make sure our content and tools are relevant and useful. Over the last 12 months, there has been a significant increase in council consents for multi-dwelling residential projects. There are now more consents issued for multi-dwelling projects than stand-alone builds.
Multi-dwelling projects are bigger, more complex, and have more layers of shared duties, creating a need for a solid health and safety plan from the very start of the build. We also consistently see that businesses that set up good processes and systems within their business and who have a strong safety culture, do better than their competitors who don’t invest in these areas.
In talking to our customers, we’ve encountered several myths about multi-dwelling projects:
In multi-dwelling projects, shared duties are unavoidable. All businesses involved must consult, cooperate, and coordinate with each other. Good communication and sharing information is critical to managing these overlapping responsibilities and creating a safe site.
To incorporate consultation, coordination, and cooperation into your construction business, start by planning each stage of the work and think about how it affects your contractors, other businesses and the public. In this process, you need to identify the risks that need to be managed and talk to who is impacted about how to handle them. With your contractors, decide who’s best to manage each risk and make sure everyone knows their roles, responsibilities, and what’s expected of them.
Compared to standalone residential projects, multi-dwelling builds involve more contractors, equipment and activities on a smaller site, which increases risks. Key considerations include:
Contractor management and the logistics of contractors on site is a major challenge on multi-dwelling projects. Successful contractor management starts before they even enter on to a site, and involves checking contractors have the right qualifications, health and safety processes, and a good track record. Pre-planning and continuous monitoring of your contractors, when they are on site, is essential to prevent injuries and ensure smooth project execution.
If you would like to know more about contractor management, check out our Simple Guide To Contractor Management.
Key high-risk areas in multi-dwelling projects create another unique challenge for these projects and can include the following:
Businesses that have good processes and systems in place do better across the board and they are more likely to complete projects on time and on budget. This creates happy clients and a better reputation in the industry.
Successful multi-dwelling projects often include:
The shift towards multi-dwelling residential projects brings new health and safety challenges. By debunking myths, understanding shared duties, managing contractors effectively, and focusing on high-risk areas, you can make your sites safer! Remember, health and safety planning is not just a regulatory requirement but a vital part of protecting the crew on site.
If you have a new project in the pipeline, let’s work together to keep your sites safe and successful. We have specifically designed Project Pro to meet the complex needs of multi-dwelling residential builds which includes extra support from our advisory team. Get in touch today!
A common question we hear is, “Do I need to fence my worksite?” The answer isn’t always straightforward. Every worksite is different, and you need to think about a few key factors to get it right.
If you’re responsible for the site, it’s up to you to make sure it’s secured from unauthorised access. A fence can help keep hazards separate from the public, but how do you know if you need one?
Ask yourself:
When deciding to fence your worksite, consider the risk factors mentioned above. If any of these are present, a fence should be used. If you can’t secure the site, you will need to enclose specific hazards when workers are not present eg. overnight
A proper worksite fence should:
These standards ensure the fence is strong, secure, and meets general safety requirements.
Excavations
If you have excavations on-site it’s important to think about how long the excavation will remain exposed. If the excavation is going to be left unattended overnight, you should consider:
Simple barricades, cones, plastic mesh netting without a solid frame, and hurdles are not enough to protect against excavation hazards. A proper safety fence is the best choice for long-term or unattended worksites with excavation risks.
Remember, when you’re away from your worksite, it’s important to protect people from hazards they might not be aware of. Simply putting up a sign is not enough. Blocking access and protecting everyone from excavation dangers shows that you’re effectively managing the risks.
You can use our handy Site Security Checklist to make sure your site is in order when it’s left unattended. If you have any questions, don’t hesitate to call HazardCo on 1800 954 702.
Adverse weather has the potential to hit hard, with strong winds, extreme temperatures, and rain. All of these factors can cause hazards for you and your workers. From trips and slips to numb fingers, heat stroke and damaged gear and equipment, varied temperatures call for specific measures to ensure that your workplace is safe.
Work doesn’t always stop when adverse weather rolls in, so it’s important to know what to do to keep your workers safe. However, if conditions become unsuitable or too dangerous, work should be paused until it is safe to continue.
Vehicle accidents don’t just happen on the roads; they can also happen within the work site. Highlight to your team that driving rules for the road also apply to your workplace, and it’s important that they take care while operating work vehicles and equipment. To make sure your vehicles and plant are safe before use, complete either a Vehicle Checklist or Pre-Start using your HazardCo App. Avoid driving if conditions are too hazardous to ensure safety.
The last thing you need is for the weather to catch you by surprise. Keep an eye on the weather forecast so your workers can prioritise the work that will be affected should the weather take a turn for the worse, and ensure they have the right gear to do the job safely.
Be vigilant when ensuring that workers are wearing proper PPE and suitable clothing when adverse weather conditions are present.
Follow these tips to optimise your crew’s safety so you can enjoy a productive season while keeping your team safe.
If you have any questions you can contact our Advisory Team on 1800 954 702.
When it comes to working at height, understanding the difference between fall prevention and fall arrest is critical. Fall prevention, also called fall restraint, stops you from being able to fall in the first place. Think of it as keeping you safely away from the edge. Fall arrest, on the other hand, is a backup plan, it doesn’t prevent the fall from happening, but catches you if one happens, reducing the risk of death to injuries that are survivable, depending on what you hit.
This blog explores fall arrest systems, covering the gear, techniques, and best practices to prevent falls or reduce injuries if a fall happens. Remember, no matter which type of equipment you use it has to be added into your SWMS. To make it even easier to follow, we’ve included short videos demonstrating each step. Let’s break it all down.
Not all gear is created equal! In fall arrest situations, quality isn’t optional – it’s life-saving. In Australia and New Zealand, fall arrest equipment must meet at least AS/NZS Standards.
Before anything else, confirm that your equipment complies with these standards, and if it’s something else like EN or ISO standards stop and ask questions, if you’re not sure who to ask then call us on 1800 954 702. Look for labels or certifications and ensure you’re using gear designed for fall arrest and not just general-purpose climbing equipment, because yes, there is a big difference!
A fall arrest system is only as strong as its weakest point. Just like building a house, the foundation must be solid. Your anchor point must be able to withstand the forces generated during a fall – this typically means being rated for at least 15kN (1,500kg) for 1 person 21kN (2,100kg) for 2 people.
Ask yourself:
Connectors are often overlooked, but they’re a vital part of your system. Use auto-locking karabiners over traditional screw gates – they’re faster to secure and less prone to accidental opening. As can be seen in the video showing the differences between manual and autolocking gates.
Be mindful of your connector positioning to avoid “roll-out.” Roll-out occurs when a karabiner rotates under pressure, such as a fall! Forcing the gate open. The video here should get you thinking…. Am I actually protected? Or do I just look protected?
The key takeaway is to ensure:
When selecting the thing between yourself and the anchor, you have three main options:
Each material type has its unique advantages and limitations, so consult an expert if you’re unsure about the best choice for your work situation.
Fall Arrest Devices come in 3 types. Most commonly you will see the “roofers kits” in the safety shops, these have a type 1 device that will move towards your anchor but not away from it without your input.
A type 2 is much like a seatbelt, they are Self Retracting Lanyards also known as SRLs, these are pretty easy to understand, and they will have their limitations printed on the device.
Type 3 fall arrest devices are like type 2 but the key difference is that they are retractable, these are what most people use for confined space entries where the entrant may have to be “winched” to safety if they pass out
All Lanyards that are the link between you and the device must include a shock absorber also known as a personal energy absorber. It’s like the brakes on a car, it slows your fall gradually, reducing the impact on your body. Without one, it would be like using a concrete wall to stop your car! Stopping that fast can generate forces over 4kN (400kg), which is enough to seriously injure or even kill by doing serious damage to your neck.
Shock absorbers are designed to limit the force put through your body to less than 4kN (400kg), protecting your neck, spine, and internal organs.
Your harness is a major piece of the puzzle, and proper fit is everything! Harnesses come in different sizes (S, M, L, XL), so check the manufacturer’s instructions for their size chart to ensure it’s the right size so you can fit it properly.
Key fitting tips:
A poorly adjusted harness can turn a fall arrest into a painful or life-threatening situation.
When working at height, it’s not just your safety that’s at stake – it’s the safety of everyone around you. One small slip of a tool can lead to serious injuries, property damage, or expensive delays.
Here’s why it matters:
In fall arrest scenarios, gravity isn’t your friend! Because your fall is uncontrolled, there’s the risk of striking whatever objects are in your path on the way down. A standard hard hat simply won’t cut it here. Use a safety helmet with a modified chin strap to keep it securely in place during a fall. A good helmet can make all the difference between walking away and serious injury that stays with you for life.
Setting up a fall arrest system isn’t just about having the right gear or looking good.
It’s about understanding how each component works together to keep you safe. Follow the steps above, inspect your equipment regularly, don’t cut corners, and never work alone when using harnesses as you will need a solid rescue plan!
If you’re unsure about which equipment is right for your situation or need help finding out about setting up your systems, get in touch with our qualified H&S advisors.
It’s better to ask questions now than face the consequences later.
We are here ready to talk when you are 1800 954 702
advisory@hazardco.com
Knowing the difference between confined spaces and restricted spaces is important for keeping everyone safe. Both can be risky, but they’re treated very differently when it comes to safety rules and legal compliance. Let’s break it down.
A confined space is a space that:
Once a space is a confined space, it stays a confined space unless all these risks are completely removed—permanently! Temporary fixes, like extra ventilation or gas testing, don’t change its classification, they are simply controls you put in place to protect yourself if you have to enter it.
Because working in confined spaces is classed as high-risk construction work, there are strict rules that will need to be followed:
A restricted space is less dangerous but still has risks. It’s an area that:
While restricted spaces aren’t always as risky as confined spaces, it’s still important to assess the situation carefully and take the right precautions for what you’re doing as they can present challenges and risks like slips/trips and body strain.
The big difference is that confined spaces are always classified as confined spaces, even when “controlled” for an entry, as their risks can’t be permanently removed. Restricted spaces don’t have the same risks related to air quality and risks of engulfment as confined spaces do. Confined spaces always need an entry permit and a rescue plan in place.
If you’re a HazardCo member and you’re unsure about a space on your site, we’re here to help. Our qualified H&S advisors can give you advice specific to your situation.
Call us on 1800 954 702 or visit www.hazardco.com for more information.