Guarding your machinery & equipment: What you need to know
Nov 17, 2021
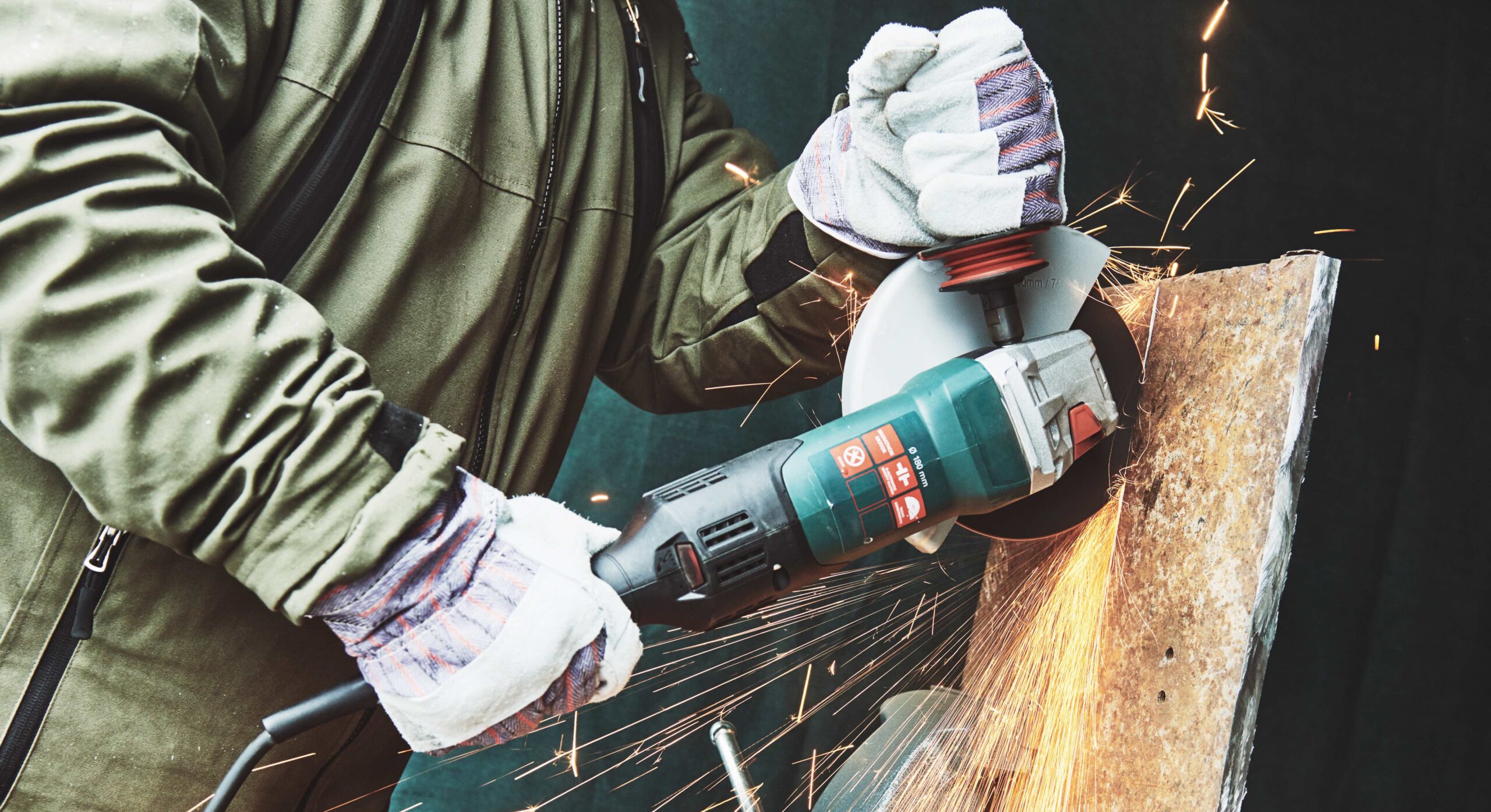
Using machinery and equipment for work on-site puts workers in close contact with powerful and fast moving tools. This makes getting the job done easier and more efficient but it does also present some risks to workers health and safety. If a worker comes into contact with machinery or equipment in an unsafe way, it can cause significant harm or injury. It is common practice to use guarding on machinery and equipment to create a barrier between the workers and the moving parts that can cause harm or injury.
Common risks and Hazards
Machinery and equipment guarding is designed to eliminate or minimise the risk of workers being harmed while completing their work. It is important to assess the hazards and risks involved with all the machinery and equipment used in the workplace. If machinery and equipment is not guarded properly, workers can sustain significant injuries due to coming in contact with moving parts.
Some common injuries are:
- Cuts
- Burns
- Electric Shocks
- Degloving
- Amputations
Because there is potential for serious harm when using machinery and equipment, it is necessary to plan a safe approach when conducting a job. This will help identify the hazards of working with machinery and equipment.
The hazard management process includes:
- Identifying hazards
- Assessing the hazard – decide if the identified hazards are significant
- Assessing the risk – decide how likely and seriously a worker could be harmed
- Controlling the hazard – either by eliminating, isolating or minimising the hazard
- Creating a hazard register to document the hazard
- Regularly reviewing and monitoring the hazards and risks.
- Create safe working methods like Standard Operating Procedures (SOP)
Choosing the right guarding
There are many different types of guards that can be used to protect workers from being harmed when using machinery and equipment. Here are some common types of guarding and examples of when they are used:
- Fixed – Screwed or fixed in place guarding to protect users from hazards. – E.g. grinders
- Interlocked – A guard that once removed or opened turns off the power to the machine by breaking a circuit. e.g. Roll formers and planing machines
- Adjustable – Safety guarding that is movable. The guard is in place to protect the user but moves to allow the function of the tool. E.g. drop saws and skill saws
- Light barriers – Usually only for manufacturing on modern machinery. Lasers or sensors can be used that once the beam is broken, can stop the hazardous machinery from operating until the beam is unbroken.
When choosing a guard, It is important to make sure the guard can actually prevent an operator from reaching into the dangerous parts of machinery and equipment. To make sure the operators are protected from the dangerous parts, the safest guarding must take into account an operator’s ability to reach into or come in contact with moving parts.
There are many different types of guards to choose from. It is important to choose guards that eliminate the potential for harm. If this is not possible, then guards should be chosen that isolate or minimise the risk to workers. It is very important that guarding is not removed or tampered with as this will increase the risk of harm to workers.
Control hierarchy:
- Elimination involves removing the risk to health and safety from the work site. It is the most effective risk control and should always be prioritised.
- Minimisation is used when a risk cannot be eliminated. This is done using: substitution, isolation, engineering, administration and PPE.
Training/ Competency
Workers should be trained to competently complete the work they are required to do. Workers should be trained and educated on the purpose and function of the different types of guarding in the workplace. Make sure that workers have the appropriate training, supervision, and qualification (if required) to safely use the necessary machinery and equipment. Keep an up-to-date register of what machinery and equipment workers are trained on and competent in using. A Training Register template is available on the HazardCo Hub which can be downloaded and filled out.
If you have any questions about guarding machinery and equipment, give HazardCo a call on 0800 555 339.