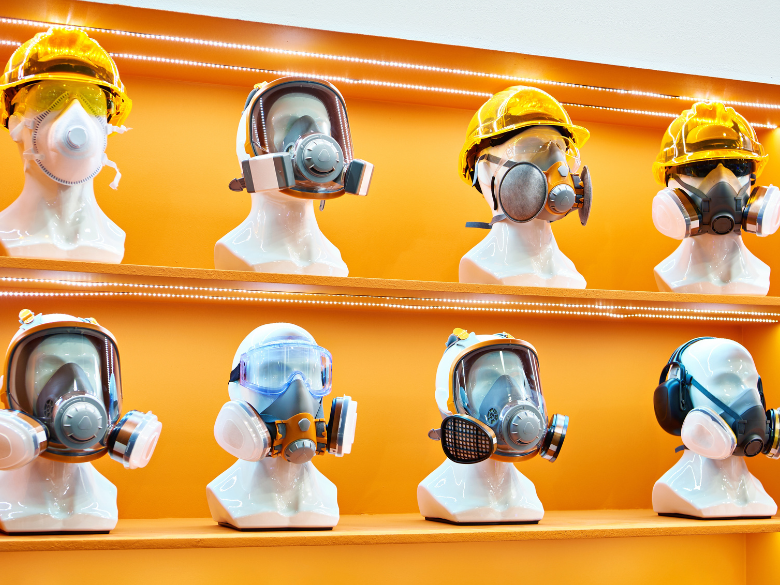
Respiratory Protective Equipment (RPE) is a critical layer of defence for workers exposed to airborne hazards like dust, fumes, vapours, But not all RPE offers equal protection, and even the best equipment won’t keep you safe if it doesn’t fit properly, isn’t suited to the task and things it’s filtering, or isn’t well maintained.
Here’s what you need to know about getting RPE right, from upfront fit testing to choosing the right cartridges, to regular check-ups and health monitoring.
Before a worker ever steps into a hazardous area, they need to be fit tested for the right RPE. Why? Because no two faces are the same. RPE comes in different sizes typically ranging from Small to Extra Large, and a poor fit can mean poor protection, even if the mask looks like it fits.
Fit testing must be:
Fit testing is also a great opportunity to train workers on how to wear and check their masks properly, which brings us to the next step.
Not all filters protect against all hazards. It’s essential to choose RPE that’s targeted to the type of contaminant and the task at hand.
To get this right, consider:
Important: Choosing the wrong size or type of RPE will give the illusion of safety, while leaving workers dangerously exposed. There is a world of difference between “looks safe” and “is safe”
Once the right gear is chosen and correctly fitted, the work doesn’t stop. RPE needs to be maintained, checked, and re-evaluated regularly.
Even with the best gear, health monitoring plays an essential role in a full respiratory protection programme. It’s how you check whether control measures (like RPE) are really working, and catch signs of harm early.
Under The Control of Substances Hazardous to Health Regulations 2002 , you’re required to monitor workers’ health if they’re exposed to substances that pose a serious health risk.
Health surveilance can include:
RPE isn’t just a piece of kit, it’s a commitment to keeping people safe. By following these three steps:
You’re doing more than following regulations. You’re creating a culture where safety is personal, proactive, and properly managed.
The right mask, worn the right way, backed by the right training and monitoring – that’s how you keep your team safe.
COSHH is a key regulation in the UK that helps protect workers and the environment from harmful substances. Managing these substances properly on-site is essential for everyone’s safety.
What are hazardous substances?
Hazardous substances can harm people or the environment. These include:
Understanding what substances are present in your workplace is crucial for ensuring safety. If you use hazardous substances at work, you must store, use, transport, and dispose of them safely to reduce risks.
What is a hazardous substances register?
A hazardous substances register is a list of all dangerous substances (and hazardous waste) used, handled, or stored at your sites. It helps you:
Keeping a COSHH register
While a COSHH register isn’t legally required, it’s a helpful tool. It’s not the same as a COSHH assessment (more on this below) but lists the substances you’ve assessed, including:
Review your register regularly to keep it accurate and up to date.
How to create a COSHH register
HazardCo members can use the Hazardous Substances Register template in the HazardCo Hub to make this process simple.
What is a Safety Data Sheet (SDS)?
An SDS provides important details about hazardous substances, such as:
It’s the business owner’s responsibility to keep SDSs updated and ensure workers can access them.
COSHH assessments
COSHH assessments are legally required for any hazardous substances. These assessments evaluate risks and outline control measures. Here’s how to do one:
Need help?
If you need support with your hazardous substances register or want more information, contact the friendly HazardCo team – we’re here to help!
Lithium batteries are common in everyday life and on the worksite, their lightweight, long life, interchangeability and quick charge benefits mean that they are now used in everything from laptops to power tools to EVs. But did you know that they pose a significant risk and need to be a part of your health and safety plan?
Lithium batteries of all sizes have the potential to overheat and catch fire. The fire is hotter, harder to put out and the smoke from these fires is incredibly toxic. Lithium batteries generally overheat if they get wet, damaged or are used with incorrect charging equipment.
Damaged batteries can explode at any time giving off flames that burn anywhere between 500 and 1000 degrees celsius. These fires are very difficult to extinguish as both water and CO2 will only suppress the fire, not extinguish it. Even if the fire has been suppressed it can still ignite again if the battery still contains energy to burn. Lithium batteries are also prone to thermal runaway, which is where one small fault can spread quickly through the battery causing a rapid increase in temperature and potential explosion.
Because of this, lithium batteries need to be properly cared for according to the manufacturer’s instructions to minimise the risk, aside from that, you need a plan in place in case of a fire.
Hot tip: The bigger the battery the bigger the risk of fire and explosion because of the increase in stored energy being released, think energy in = energy out almost instantly so take extra care with larger battery packs – like the ones in your hand held power tools.
Never dispose of Lithium batteries in general rubbish as it can result in a fire in your bin or on the way to a transfer station, creating a risk to those transporting them. The manufacturer should be able to advise safe disposal or check out your local battery recycling centre.
Lithium batteries are going to continue playing a crucial role in our workplaces and lifestyles, so it’s necessary to recognize the potential hazards associated with them. By having awareness of these risks and good practices, we can work together to reduce the potential dangers, resulting in safer working environments where Lithium batteries are used.
If you have any questions, get in touch with the Hazardco team today!
Working with heavy machinery and managing traffic on-site can be risky. But with the right checks and planning, we can keep everyone safe.
Before starting work each day, make sure your equipment is ready to go:
Visual checks (before starting the machine):
Stationary function test (with the machine on):
Moving function test:
Using your manufacturer’s checklist or the HazardCo Heavy Machinery Prestart checklist can help you cover all these points.
Keeping vehicles and people safe on-site requires a solid traffic management plan. Here’s what to consider:
Discuss this plan during site inductions so everyone knows the rules and expectations.
Heavy machinery can affect the stability of excavations if operated too close. Keep all heavy vehicles, materials, and spoil at least one meter outside the zone of influence (this may be greater depending on the ground conditions) unless specific designs support closer operations.
Uneven ground can cause machinery to tip over, leading to serious injuries. To prevent this:
If you would like more information head over to our website or to chat with one of our friendly Advisory team please give us a call on 020 4571 3920
There are over 5000 asbestos related disease deaths per year currently in the UK, including mesothelioma, lung cancer and asbestosis.
We’d like to give you some basic information on the dangers of asbestos, where it can be found and what you can do to avoid it.
There are three types of asbestos:
Inhaling asbestos fibers can cause a range of irreversible damage and diseases.
One of the most common asbestos related diseases is asbestosis. This causes severe scarring of the inner lung tissue. People usually have pain and severe difficulty breathing. Although this isn’t directly fatal in itself, it can lead to respiratory or heart failure.
Damage may occur in as little as five years, or take as long as 40-50 years after exposure for symptoms to appear. Unfortunately, many people do not realise they have been exposed until it’s too late.
It is vital you don’t attempt to remove asbestos yourself, unless you are trained, certified where required, and fully competent – we cannot stress the importance of this enough!
If you’re planning to renovate or partially demolish a building, have a survey done first to identify if Asbestos Containing Materials are present. If it is, contact a competent removal contractor.
Any building constructed up until the year 2000 has a high probability of containing asbestos. It is useful to familiarise yourself and your workers with the areas relevant to your work. If it is not expected that asbestos would be present and you see unidentified asbestos while working, stop work immediately and arrange for an assessment of the Asbestos Containing Material (ACM) to be carried out.
Yes, there is. Disposal must meet strict guidelines. Bagging and wrapping asbestos pieces is essential in any sort of removal – and dumping asbestos-containing materials can only be done in authorised locations. It is important to check with your local council for specific disposal locations and requirements. Wherever possible, leave this to the asbestos specialists.
Only a licensed contractor can remove asbestos that poses a higher risk, such as: Sprayed asbestos coatings, Asbestos lagging, Asbestos Insulating Board (AIB), and Large amounts of asbestos-containing debris or material.
Asbestos Awareness (Category A)
This training is designed for employees who may encounter asbestos during their work but do not directly work with it. It covers the basics of asbestos, its health risks, and how to identify materials that may contain asbestos (This is not adequate training for work relating to the removal of Asbestos Containing Materials)
Non-Licensed Asbestos Training (Category B)
This training is for workers who will be involved in non-licensed asbestos work, such as minor maintenance and repairs. It provides more detailed information on procedures and safety measures for handling asbestos safely
Licensed Asbestos Work (Category C)
This training is required for individuals who will be carrying out licensed asbestos removal work. It covers comprehensive procedures for safely removing asbestos, including risk assessments, safe work practices, and legal responsibilities
These training programs are crucial for ensuring the safety and health of workers who may come into contact with asbestos materials.
Recognition means everything when it comes to asbestos, signage on-site, equipping your team with knowledge of asbestos dangers, using the HazardCo App to assess risks, and educating your workers could be the difference between life and death.
Remember to also undertake health monitoring for any workers who work with airborne contaminants (such as asbestos or silica dust). Need more information?
HazardCo’s Advisory Team can help with any asbestos questions or other health and safety matters – Get in touch.
Using demolition machinery can be dangerous if it’s not handled correctly or by trained operators. Mistakes often happen when training is missed or safety checks are skipped. By making sure your team knows what to do and checking your machinery daily, you can avoid accidents and keep the worksite running smoothly. Here are some simple steps to help you use machinery safely and avoid problems.
Training and supervision
Make sure your team has the right information, training, and instructions required for the task. Having the right people involved means workers will have the skills and experience needed to complete the job safely and the task hazards will be easily identified.
Workers should be adequately trained to operate machinery. To test this knowledge, workers should be monitored and assessed regularly against operating procedures.
Pre-start checks
Always check your equipment is fit for use at the beginning of each day.
A trained and competent machinery operator should be conducting a plant/machinery pre-start check before use. This gives you the certainty that your equipment is good to go for the day and won’t cause you any unexpected problems or delays. Things to check are:
Visual checks before turning the equipment on:
Stationary function test while equipment is on:
Moving function test:
Quick hitches, safety locks and exclusion zones
Quick hitches allow you to quickly and easily change buckets or attachments on your machinery. Approximately 13% of all accidents investigated on excavators are attributed to the bucket detaching from a quick hitch device and injuring a ground worker. These are mostly fatal and major injuries. When using quick hitches and attachments you should always check the following:
Failing to check these could mean your bucket becomes detached or someone could get hit.
All quick hitches should clearly display the following information:
Quick hitches used with excavators are required to have a thorough examination by a competent person. If permanently attached this should be done 12 monthly else if not permanently attached it’s 6 monthly.
Safety locking pins need to meet the quick hitch manufacturer’s specifications and should be kept with the machinery or quick hitch device when not in use. Ensure that attachments are fitted with the correct pin centres and diameters.
Exclusion zones should be clearly marked out and all those working nearby should be informed. The hazards, risks and controls for machinery on-site should be covered in your job safety plan and shared with all on-site.
If you have any questions get in touch with the HazardCo Team today
The HazardCo App has a new Plant/Machinery Pre-Start tool! It’s a quick and easy way to do pre-start checks on various plant and machinery such as scissor lifts, boom lifts, and excavators. Just whip out your app, follow the guided prompts, and you’ll know all your reports are saved for safekeeping.
This is a great new tool for those currently filling in the log book that stays with the machine, causing lots of painful admin work to gather and compile the information for your records.
Why conduct pre-start checks?
Pre-start checks are a simple way to check that your plant and machinery are up to scratch before use. Whether it’s hired or owned equipment, a quick check will help you to identify any potential issues that could impact the safety of your team or the performance of the machinery. By referring to the manufacturer’s instructions and best practices, workers can make sure the machinery they have is in a safe condition to be used, and if not, the HazardCo App gives you an easy way to communicate the issues happening on the ground to the right people. When done well, pre-start checks go a long way to preventing incidents and equipment failures.
When to use the Plant/Machinery Pre-Start tool
The Plant/Machinery Pre-Start tool should be used before the operation of any plant or machinery. You can find it in the main menu of the HazardCo App. Once a pre-start check is completed, the report is automatically saved to the Reports section in the Hub and the App for easy access in the future.
Benefits for workers: The Plant/Machinery Pre-Start tool provides an easy way to follow pre-start procedures. It helps you communicate any issues that need to go up the chain and make sure information isn’t lost or misunderstood.
Benefits for workers: This tool is a quicker and easier way to maintain evidence of your team’s safe work practices on-site. Anyone on-site can use the HazardCo App to complete a Plant/Machinery pre-start, you’ll be able to see it’s been done, and you won’t need to find and scan physical log books anymore!
We get it — figuring out what to do after an incident or near miss on-site can feel a bit overwhelming. One of the most common things our Advisory Team hears is, “Do I need to report this?” If it’s a notifiable event, you have a legal duty to let the Health and Safety Executive (HSE) know under Reporting of Injuries, Diseases and Dangerous Occurrences Regulations (RIDDOR) – Sounds like a lot of paperwork right? Not with HazardCo, our App makes it easy to log an incident or near miss and we’re here to guide you with what to do next!
Let’s break down RIDDOR in plain language. It’s basically the UK’s system for tracking workplace incidents and near misses.
RIDDOR stands for Reporting of Injuries, Diseases and Dangerous Occurrences Regulations. It’s the rules about which workplace incidents you need to tell the authorities about.
Every time you report an incident or near miss, you’re helping make the site safer. It’s not about pointing fingers — it’s about learning from what happened and stopping it from happening again. Everyone on-site has the right to know about any risks, and we all play a part in keeping each other safe.
Creating a culture where everyone feels comfortable reporting issues means better communication and fewer surprises.
It’s easy:
Your report is saved in the Hub and kept on file while you’re a HazardCo member
The App will prompt you to give us a call if needed. Our Advisory Team gets a copy and will:
We recommend:
Keep records
You’re legally required to keep these records for at least 3 years. Logging everything in the App means it’s all saved in the Hub, organised and easy to access if you ever need it.
No one wants incidents to happen on site, but being prepared makes all the difference. Stay calm, follow the steps, and give us a call if you’re unsure. Our Advisory team is available 24/7 for serious incidents.
Got a question? Reach out to us today — we’re here to help.
Hand and finger injuries are one of the most common injuries on-site. Over the last year, HazardCo has received 4599 incident reports – 720 of those were hand or finger injuries. That highlights just how often these injuries happen, so let’s look at how they happen and what we can do to prevent them.
There are plenty of ways hands and fingers can get hurt on-site, but the most common injuries include:
These injuries happen due to faulty equipment, falling objects, getting caught between materials, electrical issues, and simple mistakes.
Many hand and finger injuries occur from everyday tools such as hammers, saws, pliers,utility knives and circular saws, and nail guns. These injuries are often caused by rushing, fatigue, complacency, using damaged tools, or not having the right training.
Hand injuries aren’t just painful – they affect your ability to work and go about your daily life. Even minor injuries can weaken grip strength and finger movement. More serious injuries could mean permanent damage or loss of function.
Keeping hands safe is all about awareness and good habits. Here’s how you and your team can reduce the risk:
Safety isn’t just about following the rules. It’s about actions and leading by example. Leaders set the tone by demonstrating safe practices, sharing real stories of how hand injuries can impact lives and actively monitoring worksite conditions. Once workers understand the risk, it’s their responsibility to stay aware, but team leaders must make sure safety measures are in place and consistently followed.
Let’s work together to bring those hand injury numbers down!
Got a question about hand safety or any other health and safety issue? The HazardCo Advisory Team is here to help – call 020 4571 3920
It’s never good to find out the hard way that there was a gas, power, water, or communications line buried right where you needed to put something on your site! Safe excavation practices help you to get through the work without injury and avoid hitting critical services.
Digging blind is not the best way forward for your schedule or your safety, so we have put together some key notes for you to bear in mind when excavating to help save you some costs, time and help you avoid tragedy.
Excavation work is any work involving the removal of soil or rock from a site to form an open face, hole or cavity, using tools, machinery or explosives. This includes open excavations, potholing, pit excavations, trenches, retaining walls and shafts and drives.
Employers have a legal duty of care to take reasonable actions to protect both the people and the services which may be affected by their work. Getting and using the appropriate information on the services is an important part of ensuring safe excavation on your site. There is a large range of options this can cover, so we will cover the basics in this article.
If you have more complex excavations and want advice then get in contact with us.
Remember any ground disturbance regardless of depth can damage infrastructure networks like gas, water, electricity so you need to get the right information to keep you & the utilities safe.
Before you start digging, you need to know what’s below the surface. Use Linesearch Before U Dig – a free online service that helps you check for underground assets from over 140 asset owners. However, keep in mind that not all asset owners are part of Linesearch. This means you might need to contact other organizations like the local roads authority, street lighting authority, or National Grid to get their plans and information.
Key Reminder:
Any digging can damage underground infrastructure, so take your time, follow the process, and stay safe!
A safe system of work has three key steps:
Once services are exposed, protect them by:
Key Reminder: Always follow the steps and stay vigilant—digging safely protects everyone on-site!
If you’ve got a question about safe excavation or any other health and safety matter, the HazardCo Advisory Team is here to help. Give them a call on 020 4571 3920
The Linesearch before u dig website has a tonne of resources available With over 275,000 registered Users representing utility companies, contractors, councils, landowners and the public. The Health and Safety Executive (HSE) also have the HSG47 document which offers guidance on how to avoid underground services.