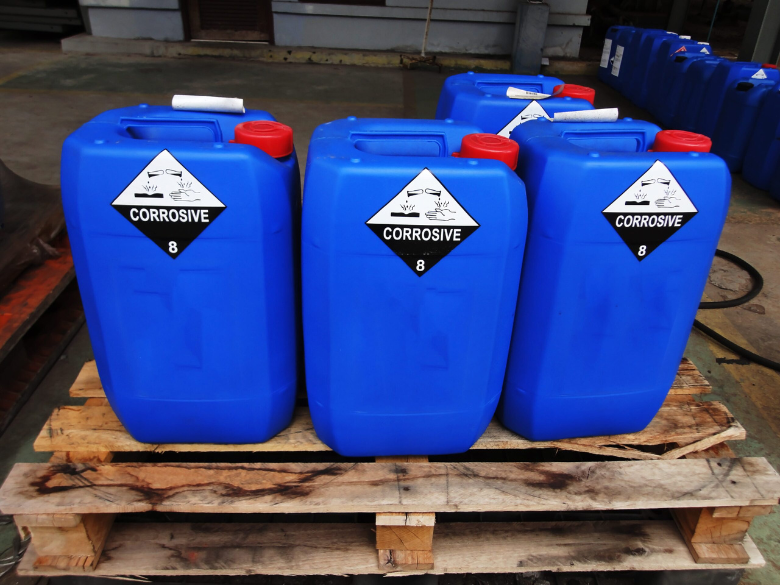
COSHH is a key regulation in the UK that helps protect workers and the environment from harmful substances. Managing these substances properly on-site is essential for everyone’s safety.
What are hazardous substances?
Hazardous substances can harm people or the environment. These include:
Understanding what substances are present in your workplace is crucial for ensuring safety. If you use hazardous substances at work, you must store, use, transport, and dispose of them safely to reduce risks.
What is a hazardous substances register?
A hazardous substances register is a list of all dangerous substances (and hazardous waste) used, handled, or stored at your sites. It helps you:
Keeping a COSHH register
While a COSHH register isn’t legally required, it’s a helpful tool. It’s not the same as a COSHH assessment (more on this below) but lists the substances you’ve assessed, including:
Review your register regularly to keep it accurate and up to date.
How to create a COSHH register
HazardCo members can use the Hazardous Substances Register template in the HazardCo Hub to make this process simple.
What is a Safety Data Sheet (SDS)?
An SDS provides important details about hazardous substances, such as:
It’s the business owner’s responsibility to keep SDSs updated and ensure workers can access them.
COSHH assessments
COSHH assessments are legally required for any hazardous substances. These assessments evaluate risks and outline control measures. Here’s how to do one:
Need help?
If you need support with your hazardous substances register or want more information, contact the friendly HazardCo team – we’re here to help!
Lithium batteries are common in everyday life and on the worksite, their lightweight, long life, interchangeability and quick charge benefits mean that they are now used in everything from laptops to power tools to EVs. But did you know that they pose a significant risk and need to be a part of your health and safety plan?
Lithium batteries of all sizes have the potential to overheat and catch fire. The fire is hotter, harder to put out and the smoke from these fires is incredibly toxic. Lithium batteries generally overheat if they get wet, damaged or are used with incorrect charging equipment.
Damaged batteries can explode at any time giving off flames that burn anywhere between 500 and 1000 degrees celsius. These fires are very difficult to extinguish as both water and CO2 will only suppress the fire, not extinguish it. Even if the fire has been suppressed it can still ignite again if the battery still contains energy to burn. Lithium batteries are also prone to thermal runaway, which is where one small fault can spread quickly through the battery causing a rapid increase in temperature and potential explosion.
Because of this, lithium batteries need to be properly cared for according to the manufacturer’s instructions to minimise the risk, aside from that, you need a plan in place in case of a fire.
Hot tip: The bigger the battery the bigger the risk of fire and explosion because of the increase in stored energy being released, think energy in = energy out almost instantly so take extra care with larger battery packs – like the ones in your hand held power tools.
Never dispose of Lithium batteries in general rubbish as it can result in a fire in your bin or on the way to a transfer station, creating a risk to those transporting them. The manufacturer should be able to advise safe disposal or check out your local battery recycling centre.
Lithium batteries are going to continue playing a crucial role in our workplaces and lifestyles, so it’s necessary to recognize the potential hazards associated with them. By having awareness of these risks and good practices, we can work together to reduce the potential dangers, resulting in safer working environments where Lithium batteries are used.
If you have any questions, get in touch with the Hazardco team today!
Working with heavy machinery and managing traffic on-site can be risky. But with the right checks and planning, we can keep everyone safe.
Before starting work each day, make sure your equipment is ready to go:
Visual checks (before starting the machine):
Stationary function test (with the machine on):
Moving function test:
Using your manufacturer’s checklist or the HazardCo Heavy Machinery Prestart checklist can help you cover all these points.
Keeping vehicles and people safe on-site requires a solid traffic management plan. Here’s what to consider:
Discuss this plan during site inductions so everyone knows the rules and expectations.
Heavy machinery can affect the stability of excavations if operated too close. Keep all heavy vehicles, materials, and spoil at least one meter outside the zone of influence (this may be greater depending on the ground conditions) unless specific designs support closer operations.
Uneven ground can cause machinery to tip over, leading to serious injuries. To prevent this:
If you would like more information head over to our website or to chat with one of our friendly Advisory team please give us a call on 020 4571 3920
There are over 5000 asbestos related disease deaths per year currently in the UK, including mesothelioma, lung cancer and asbestosis.
We’d like to give you some basic information on the dangers of asbestos, where it can be found and what you can do to avoid it.
There are three types of asbestos:
Inhaling asbestos fibers can cause a range of irreversible damage and diseases.
One of the most common asbestos related diseases is asbestosis. This causes severe scarring of the inner lung tissue. People usually have pain and severe difficulty breathing. Although this isn’t directly fatal in itself, it can lead to respiratory or heart failure.
Damage may occur in as little as five years, or take as long as 40-50 years after exposure for symptoms to appear. Unfortunately, many people do not realise they have been exposed until it’s too late.
It is vital you don’t attempt to remove asbestos yourself, unless you are trained, certified where required, and fully competent – we cannot stress the importance of this enough!
If you’re planning to renovate or partially demolish a building, have a survey done first to identify if Asbestos Containing Materials are present. If it is, contact a competent removal contractor.
Any building constructed up until the year 2000 has a high probability of containing asbestos. It is useful to familiarise yourself and your workers with the areas relevant to your work. If it is not expected that asbestos would be present and you see unidentified asbestos while working, stop work immediately and arrange for an assessment of the Asbestos Containing Material (ACM) to be carried out.
Yes, there is. Disposal must meet strict guidelines. Bagging and wrapping asbestos pieces is essential in any sort of removal – and dumping asbestos-containing materials can only be done in authorised locations. It is important to check with your local council for specific disposal locations and requirements. Wherever possible, leave this to the asbestos specialists.
Only a licensed contractor can remove asbestos that poses a higher risk, such as: Sprayed asbestos coatings, Asbestos lagging, Asbestos Insulating Board (AIB), and Large amounts of asbestos-containing debris or material.
Asbestos Awareness (Category A)
This training is designed for employees who may encounter asbestos during their work but do not directly work with it. It covers the basics of asbestos, its health risks, and how to identify materials that may contain asbestos (This is not adequate training for work relating to the removal of Asbestos Containing Materials)
Non-Licensed Asbestos Training (Category B)
This training is for workers who will be involved in non-licensed asbestos work, such as minor maintenance and repairs. It provides more detailed information on procedures and safety measures for handling asbestos safely
Licensed Asbestos Work (Category C)
This training is required for individuals who will be carrying out licensed asbestos removal work. It covers comprehensive procedures for safely removing asbestos, including risk assessments, safe work practices, and legal responsibilities
These training programs are crucial for ensuring the safety and health of workers who may come into contact with asbestos materials.
Recognition means everything when it comes to asbestos, signage on-site, equipping your team with knowledge of asbestos dangers, using the HazardCo App to assess risks, and educating your workers could be the difference between life and death.
Remember to also undertake health monitoring for any workers who work with airborne contaminants (such as asbestos or silica dust). Need more information?
HazardCo’s Advisory Team can help with any asbestos questions or other health and safety matters – Get in touch.
Using demolition machinery can be dangerous if it’s not handled correctly or by trained operators. Mistakes often happen when training is missed or safety checks are skipped. By making sure your team knows what to do and checking your machinery daily, you can avoid accidents and keep the worksite running smoothly. Here are some simple steps to help you use machinery safely and avoid problems.
Training and supervision
Make sure your team has the right information, training, and instructions required for the task. Having the right people involved means workers will have the skills and experience needed to complete the job safely and the task hazards will be easily identified.
Workers should be adequately trained to operate machinery. To test this knowledge, workers should be monitored and assessed regularly against operating procedures.
Pre-start checks
Always check your equipment is fit for use at the beginning of each day.
A trained and competent machinery operator should be conducting a plant/machinery pre-start check before use. This gives you the certainty that your equipment is good to go for the day and won’t cause you any unexpected problems or delays. Things to check are:
Visual checks before turning the equipment on:
Stationary function test while equipment is on:
Moving function test:
Quick hitches, safety locks and exclusion zones
Quick hitches allow you to quickly and easily change buckets or attachments on your machinery. Approximately 13% of all accidents investigated on excavators are attributed to the bucket detaching from a quick hitch device and injuring a ground worker. These are mostly fatal and major injuries. When using quick hitches and attachments you should always check the following:
Failing to check these could mean your bucket becomes detached or someone could get hit.
All quick hitches should clearly display the following information:
Quick hitches used with excavators are required to have a thorough examination by a competent person. If permanently attached this should be done 12 monthly else if not permanently attached it’s 6 monthly.
Safety locking pins need to meet the quick hitch manufacturer’s specifications and should be kept with the machinery or quick hitch device when not in use. Ensure that attachments are fitted with the correct pin centres and diameters.
Exclusion zones should be clearly marked out and all those working nearby should be informed. The hazards, risks and controls for machinery on-site should be covered in your job safety plan and shared with all on-site.
If you have any questions get in touch with the HazardCo Team today
We get it — figuring out what to do after an incident or near miss on-site can feel a bit overwhelming. One of the most common things our Advisory Team hears is, “Do I need to report this?” If it’s a notifiable event, you have a legal duty to let the Health and Safety Executive (HSE) know under Reporting of Injuries, Diseases and Dangerous Occurrences Regulations (RIDDOR) – Sounds like a lot of paperwork right? Not with HazardCo, our App makes it easy to log an incident or near miss and we’re here to guide you with what to do next!
Let’s break down RIDDOR in plain language. It’s basically the UK’s system for tracking workplace incidents and near misses.
RIDDOR stands for Reporting of Injuries, Diseases and Dangerous Occurrences Regulations. It’s the rules about which workplace incidents you need to tell the authorities about.
Every time you report an incident or near miss, you’re helping make the site safer. It’s not about pointing fingers — it’s about learning from what happened and stopping it from happening again. Everyone on-site has the right to know about any risks, and we all play a part in keeping each other safe.
Creating a culture where everyone feels comfortable reporting issues means better communication and fewer surprises.
It’s easy:
Your report is saved in the Hub and kept on file while you’re a HazardCo member
The App will prompt you to give us a call if needed. Our Advisory Team gets a copy and will:
We recommend:
Keep records
You’re legally required to keep these records for at least 3 years. Logging everything in the App means it’s all saved in the Hub, organised and easy to access if you ever need it.
No one wants incidents to happen on site, but being prepared makes all the difference. Stay calm, follow the steps, and give us a call if you’re unsure. Our Advisory team is available 24/7 for serious incidents.
Got a question? Reach out to us today — we’re here to help.
Hand and finger injuries are one of the most common injuries on-site. Over the last year, HazardCo has received 4599 incident reports – 720 of those were hand or finger injuries. That highlights just how often these injuries happen, so let’s look at how they happen and what we can do to prevent them.
There are plenty of ways hands and fingers can get hurt on-site, but the most common injuries include:
These injuries happen due to faulty equipment, falling objects, getting caught between materials, electrical issues, and simple mistakes.
Many hand and finger injuries occur from everyday tools such as hammers, saws, pliers,utility knives and circular saws, and nail guns. These injuries are often caused by rushing, fatigue, complacency, using damaged tools, or not having the right training.
Hand injuries aren’t just painful – they affect your ability to work and go about your daily life. Even minor injuries can weaken grip strength and finger movement. More serious injuries could mean permanent damage or loss of function.
Keeping hands safe is all about awareness and good habits. Here’s how you and your team can reduce the risk:
Safety isn’t just about following the rules. It’s about actions and leading by example. Leaders set the tone by demonstrating safe practices, sharing real stories of how hand injuries can impact lives and actively monitoring worksite conditions. Once workers understand the risk, it’s their responsibility to stay aware, but team leaders must make sure safety measures are in place and consistently followed.
Let’s work together to bring those hand injury numbers down!
Got a question about hand safety or any other health and safety issue? The HazardCo Advisory Team is here to help – call 020 4571 3920
It’s never good to find out the hard way that there was a gas, power, water, or communications line buried right where you needed to put something on your site! Safe excavation practices help you to get through the work without injury and avoid hitting critical services.
Digging blind is not the best way forward for your schedule or your safety, so we have put together some key notes for you to bear in mind when excavating to help save you some costs, time and help you avoid tragedy.
Excavation work is any work involving the removal of soil or rock from a site to form an open face, hole or cavity, using tools, machinery or explosives. This includes open excavations, potholing, pit excavations, trenches, retaining walls and shafts and drives.
Employers have a legal duty of care to take reasonable actions to protect both the people and the services which may be affected by their work. Getting and using the appropriate information on the services is an important part of ensuring safe excavation on your site. There is a large range of options this can cover, so we will cover the basics in this article.
If you have more complex excavations and want advice then get in contact with us.
Remember any ground disturbance regardless of depth can damage infrastructure networks like gas, water, electricity so you need to get the right information to keep you & the utilities safe.
Before you start digging, you need to know what’s below the surface. Use Linesearch Before U Dig – a free online service that helps you check for underground assets from over 140 asset owners. However, keep in mind that not all asset owners are part of Linesearch. This means you might need to contact other organizations like the local roads authority, street lighting authority, or National Grid to get their plans and information.
Key Reminder:
Any digging can damage underground infrastructure, so take your time, follow the process, and stay safe!
A safe system of work has three key steps:
Once services are exposed, protect them by:
Key Reminder: Always follow the steps and stay vigilant—digging safely protects everyone on-site!
If you’ve got a question about safe excavation or any other health and safety matter, the HazardCo Advisory Team is here to help. Give them a call on 020 4571 3920
The Linesearch before u dig website has a tonne of resources available With over 275,000 registered Users representing utility companies, contractors, councils, landowners and the public. The Health and Safety Executive (HSE) also have the HSG47 document which offers guidance on how to avoid underground services.
Worksites tend to be filled with constant noise from tools and machinery. Work-related hearing loss is a real threat for many who spend the majority of their working lives on-site. While noise often means things are getting done, there is a downside to it. Hazardous noise can affect a worker’s physical and mental wellbeing including hearing loss, stress, and lower productivity. So to help you protect your hearing, here are a few helpful tips to manage noise.
The aim of the Noise Regulations is to ensure that workers’ hearing is protected from excessive noise at their place of work, which could cause them to lose their hearing and/or to suffer from tinnitus (permanent ringing in the ears).
Employers must assess the risk to workers when noise is above is 80dB(A) and employers MUST ensure hearing protection is worn when noise is 85 dB(A).
Understanding what makes noise on-site, and how it impacts people and different areas on site is critical. Ask yourself and your workers:
Once you understand the answers to the above, you can start putting plans and checks in place to monitor noise on-site.
Be sure to review the plan throughout the project, as different stages will create varying levels of noise.
The most effective way to reduce noise is to eliminate its source, though this isn’t always possible.
Regular maintenance of equipment is another effective method to minimise noise production. Proper upkeep can significantly lower noise levels.
The HSE has also suggested alternative methods to decrease noise on-site, including:
Additionally, limiting the time spent in noisy areas will significantly reduce exposure.
Isolation involves creating a dedicated space for ‘noisy work’. This could be an enclosed room or area of site where all noisy work and machinery is used. This helps manage the noise by blocking the path of noise and reducing the levels that reach your team.
Having a good understanding of how machinery and tools operate can help modify processes to reduce noise at the source. Engineering controls can include choosing attachments or parts that are noise reducing, or changing the way machinery and tools are used.
Perfect for when you are running a large generator or a dedicated workspace, acoustic enclosures help to trap the noise within its barriers. Setting up an acoustic enclosure that has 2 or 3 barriers/ walls can reduce noise.
What makes a quality acoustic enclosure:
With noise comes vibrations. These vibrations can be just as harmful as the noise itself. Here are a few strategies to help decrease vibrations when using machines or power tools:
It’s not possible to escape noise on-site, however we can manage noise and put steps in place to help reduce the effect that it has on us while we’re working.
If you have any questions don’t forget to reach out to the team!
Respiratory Protection Equipment (RPE) is essential gear for protecting you from inhaling hazardous substances. In this blog, we’ll explore the important role of RPE, whether you are dealing with airborne contaminants like asbestos, fumes, or dust, RPE is an essential protective equipment (PPE) that makes sure you can breathe safely. Join us as we deep dive into the different types of RPE, their applications, and how they can protect you from potential health risks.
Before you even get started with RPE, make sure you have other practical control measures in place first; such as local exhaust ventilation or direct dust-extracted tools with a vacuum catchment to get rid of the majority of contaminants in the air. You should also be keeping an eye on your team’s health and workplace conditions to ensure that, over time, they aren’tbecomign unwell or getting injured by their work.
Remember, there is no such thing as healthy dust, even if you are outside!
We’ve gone ahead and put together a quick guide of factors to consider when providing your workers with RPE.
RPE should be the last resort to protect against harmful dust. Before work starts, look at ways of stopping or reducing the amount of dust you might make. Even if you stop some dust this way, you may do other work that could still produce high dust levels. In these cases the most important action is to stop the dust getting into the air with either water or extraction.
Water or on-tool extraction may not always be appropriate or they might not reduce exposure enough. Often respiratory protection (RPE) has to be provided as well. You will need to make sure that the RPE is:
adequate for the amount and type of dust – RPE has an assigned protection factor (APF) which shows how much protection it gives the wearer. The general level for construction dust is an APF of 20. This means the wearer only breathes one twentieth of the amount of dust in the air;
Respirators use replaceable filters to remove contaminants to clean the air for the wearer. They come in disposable, half-face and full-face versions. The cartridge filters are specific to certain types of contaminants, ask your manufacturer exactly which cartridge you should be using for the respirator you have and the contaminants you will be facing.
Remember if you have stubble or any facial hair you may not be getting the seal and the protection you think you are! So if you love your beard as much as your lungs read on to find out what you can do.
Powered air purifying respirators (PAPRs)
Are made up of headgear and fan assembly that take contaminated air, filter it, and then delivers the clean air to the user. These are also known as positive pressure systems. These not only keep you nice and cool but offer the highest protection there is for people who have facial hair. Something to note with these is that the visors and headset can be impact rated if you need it, and don’t fog up because of the airflow.
Supplied air respirators
Provide a supply of clean air to the wearer from a source such as an air compressor or cylinder. It’s important to note that the air supply needs to be checked regularly to make sure that it is safe to use – just think about what you see coming out of your air compressor when you release the valve under the air tank! The user must also be trained in how to use the system.
It’s important for your workers to visually check their RPE for signs of damage before each use to identify any issues, including whether it needs to be cleaned or decontaminated.
Make sure your team keeps their RPE on while working in the hazardous area. Removing it for even a short period of time is a risk to their health.
Did you know that they come in different sizes? One size does not fit all!
Everyone’s face is different, so one size doesn’t fit all when it comes to RPE. If a mask doesn’t fit properly, it won’t do its job, which could lead to serious health issues. Fit testing helps make sure the mask forms a proper seal and keeps harmful particles out. It also helps identify which masks aren’t suitable for certain workers. The manufacturer of the RPE can tell you who can do this testing.
There are two checks which you need to do each time you use RPE:
Keep in mind that if your workers’ safety glasses fog up while they are wearing a half-face respirator, this is a sign that there is a leak at the top of the respirator which means they are not getting full protection.
If your crew is wearing respiratory protective equipment (RPE), they need to be clean-shaven. Even a bit of stubble can stop the mask from sealing properly, which means they’re still breathing in harmful dust and chemicals. A proper fit and the right RPE for the job go hand in hand.
A recent study tested different masks on 15 guys, checking the fit right after shaving and again over the next week. The results? Stubble started affecting the seal within 24 hours and got worse as the hair grew. That means protection can drop fast, putting workers at risk.
As an employer, it’s your responsibility to monitor your team’s health. Make sure you’re doing regular Site Reviews using the HazardCo App to spot risks and put proper controls in place. If you need a hand, the HazardCo Support Team is here to help—just reach out!
Got any questions? Reach out to the HazardCo Team