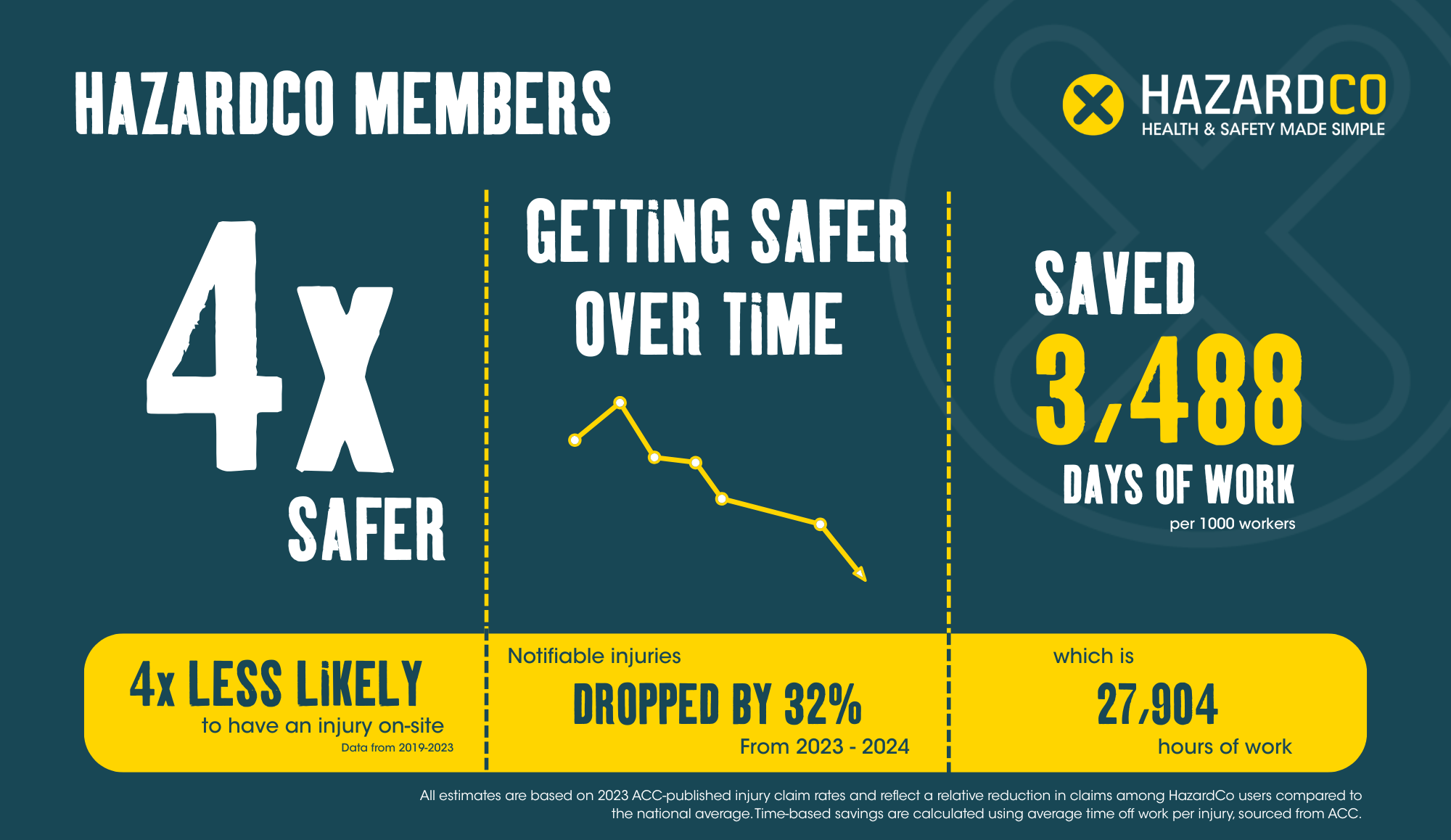
At HazardCo, we’re all about making health and safety simple – and it’s working. New data shows that our members are safer on site compared to the national average. Whether you’re on the tools or managing a team, these numbers show the real impact of doing health and safety the HazardCo way.
There’s a big difference between having a health and safety system and using one that actually works.
At HazardCo, we don’t just help you tick boxes. Our guided tools make it easy to follow the right health and safety steps at the right time, and when that happens, sites are safer. Now we’ve got the data to back it up.
New stats show that HazardCo members are significantly safer on site than the national average. Whether you’re on the tools or running the business, this proves that doing health and safety the HazardCo way pays off.
We’ve crunched the numbers and here’s what we found:
That’s a massive difference.
Why it’s working
Our digital tools make it easy to manage health and safety day to day. From guided Site Reviews that help you put the right controls in place, to risk assessments, toolbox talks, site inductions, and incident reports — it’s all handled in the HazardCo App.
Everyone on site can get involved, making it easier to spot risks early, take action, and keep things running smoothly. Plus, if something does go sideways, our expert advisors are available 24/7 to help you respond the right way.
When health and safety is easy to follow and part of your everyday routine, it becomes second nature – and it keeps people safer.
Fewer injuries mean less time off the tools, and that saves your business money. When your team stays safe, you avoid costly downtime, keep your jobs on track, and reduce the chance of ACC claims or needing to bring in extra workers to cover.
You’ll also be in a better position if WorkSafe ever comes knocking. HazardCo helps you meet your legal responsibilities and show you’re doing things properly, without the paperwork pile-up.
A well-run site is a safer site. It’s better for your crew, your schedule, and your bottom line.
Using HazardCo isn’t just about ticking boxes faster, it’s about making your site genuinely safer.
You’re working smarter, with fewer accidents, less downtime, and more time getting the job done right.
Our mission is to keep the person at the top of the ladder safe, and the data shows it’s working.
Not a member yet? Maybe it’s time to make the switch.
There’s major HR changes on the way for how Kiwi businesses manage contractors, and if you run a construction company, are a tradie, or work with subcontractors, this is something you need to pay attention to.
The government is introducing a new “contractor certainty test,” a legal tool that will help determine whether someone is a true independent contractor or should legally be considered an employee.
Right now, it’s possible for someone to sign on as a contractor but later challenge that status in court, claiming they were really an employee (and are owed sick leave, holiday pay, etc). That’s led to uncertainty for business owners who thought they were doing the right thing.
This new test will make things clearer but also puts more responsibility on employers to get it right from the start.
If your independent contractor agreement meets the criteria in the new law (expected later in 2025), the contractor won’t be able to challenge it in court. But if it doesn’t meet the bar, they can and that could open your business up to risk.
Until we know more about how the criteria will be applied and when the new law will take effect, the risk of claims remains.
However, the Government has signalled that one of the elements of the new test will be that a written independent contractor agreement must be in place.
That’s why we are urging businesses to review their contracts now.
Who’s affected?
If you’re in construction or trades, you likely have a mix of employees and contractors on your books. Getting this wrong could mean fines, backpay claims, and a whole lot of hassle you don’t need.
Final thought
This new legislation isn’t about making life harder, it’s about giving both businesses and workers clarity. But it does mean you need to be proactive by documenting your working relationships.
We’ll keep you posted as we learn more about the law change before it comes into effect.
Got questions? Talk to your HR advisor or use a tool like Employr to sort your agreements.
Hand and finger injuries are one of the most common injuries on-site. Over the last year, HazardCo has received 4599 incident reports – 720 of those were hand or finger injuries. That highlights just how often these injuries happen, so let’s look at how they happen and what we can do to prevent them.
There are plenty of ways hands and fingers can get hurt on-site, but the most common injuries include:
These injuries happen due to faulty equipment, falling objects, getting caught between materials, electrical issues, and simple mistakes.
Many hand and finger injuries occur from everyday tools such as hammers, saws, pliers and utility knives. These injuries are often caused by rushing, fatigue, complacency, using damaged tools, or not having the right training.
Hand injuries aren’t just painful – they affect your ability to work and go about your daily life. Even minor injuries can weaken grip strength and finger movement. More serious injuries could mean permanent damage or loss of function.
Keeping hands safe is all about awareness and good habits. Here’s how you and your team can reduce the risk:
Safety isn’t just about following the rules. It’s about actions and leading by example. Leaders set the tone by demonstrating safe practices, sharing real stories of how hand injuries can impact lives and actively monitoring worksite conditions. Once workers understand the risk, it’s their responsibility to stay aware, but team leaders must make sure safety measures are in place and consistently followed.
Let’s work together to bring those hand injury numbers down!
Got a question about hand safety or any other health and safety issue? The HazardCo Advisory Team is here to help – call 0800 555 339
You might have heard that the government is making some changes to the Health and Safety Work Act (HSWA). But what does that mean for your building company or trade business?
The announcements this week are part of a broader reform, and we expect more decisions and updates over the coming months. So far, the announcements are focused on reducing compliance costs for low-risk industries. Here’s the key: the construction industry is still high-risk, and these health & safety changes won’t impact your core safety responsibilities.
The government’s proposed changes are currently aimed at businesses that don’t face the same risks as the construction sector. For builders and tradies, the rules around working at heights, machinery operation, and handling hazardous materials remain unchanged. Your responsibility to keep your team safe stays the same.
Construction still has high injury and fatality rates. Right now, New Zealand workers are twice as likely to be killed on the job compared to Australian workers. These stats show there’s still a lot to be done to improve in the industry, which is why keeping safety a top priority on-site is so important.
While some industries may see relaxed regulations, health and safety in construction will always be complex. That’s where we come in. We’re on your side, helping you navigate through the changes and ensuring you stay compliant while keeping your workers safe—no matter what the government does next. Our advisory team is always available to chat about these changes, so don’t hesitate to give us a call.
Minister for Workplace Relations and Safety, Brooke van Velden, has stated that these reforms are just the beginning. Legislation to amend the Health and Safety at Work Act is expected to be introduced by the end of the year, with the intention of passing it in early 2026. But for now, you don’t need to worry about major shifts affecting your business. The key rules—the ones that protect your team—will stay the same.
We’re here to help you stay ahead of these changes. If you have any questions or need advice on how these changes may impact you, reach out to our team. We’re always ready to assist in keeping your workers safe and your business running smoothly.
Farming is the backbone of New Zealand, providing food, jobs, and a connection to our land. However, it’s also one of the most hazardous industries in the country. In 2023, over 18,400 farming-related injury claims were accepted by ACC, costing more than $107 million in recovery efforts.
Recognising the pressing need to improve safety, ACC has partnered with Safer Farms, investing over $11 million in the “Farm Without Harm” strategy. This five-year plan aims to reduce injuries and fatalities by implementing practical safety measures directly on farms.
When someone new comes to your farm – whether it’s a worker, contractor or visitor – take 15 minutes to show them around. Point out hazards, emergency meeting points, and the basics they need to stay safe. This small investment of time could save a life.
A safe farm is a successful farm. By putting health and safety first, you’re not just protecting yourself and your team – you’re securing the future of your business and New Zealand’s agricultural sector. Let’s work together to make our farms safer for everyone.
If you have any questions, get in touch with the team.
Machinery is a big part of manufacturing, but if it’s not used safely, it can cause serious injuries – or worse. WorkSafe NZ has seen too many cases where unsafe machines have led to lost fingers, crushed hands, and hefty fines for businesses. The good news? Most of these incidents are preventable with the right safety measures.
Here’s the good news: most of these accidents are completely preventable with some straightforward safety measures.
Let’s talk about what actually makes machines dangerous. It’s rarely the machine itself, but how we use, maintain, and protect it:
The cost of ignoring safety far outweighs the investment in getting it right. WorkSafe NZ provides excellent guidance to help businesses implement effective safety measures that protect both people and productivity.
Creating a safer workplace doesn’t require a complete factory overhaul. These five practical steps will make a real difference:
1. Do regular safety checks
Take a 15-minute walk around your site each week. Look for opportunities to improve guarding, reduce exposure to moving parts, or address signs of wear. Encourage your workers to share their insights – they often have the best suggestions for improvements.
2. Use proper guarding
Guards are as important to your machinery as any other component. Make it standard practice to keep guards in place and properly adjusted. If one needs repair, or is missing, stop using the machine until it is fixed
3. Train your team
Knowledgeable operators are your best asset when it comes to getting the most from your equipment. Take time to ensure everyone knows the basics – how to properly start up and shut down each machine, where to find emergency stops, when adjustments might be needed, and the daily best practices that keep things running smoothly. Refresher training doesn’t take long and can make a world of difference, boosting your worker’s confidence and performance on the floor. It’s a small investment in time that pays off in better quality work, and fewer disruptions and incidents.
4. Lock it out before maintenance
When equipment needs attention, a simple lockout/tagout routine keeps everyone safe and your machinery in shape. Just follow these lockout/tagout steps in order: properly shut down the machine, disconnect its power source, attach a tag with the maintenance person’s name, double-check that it won’t start unexpectedly, complete the work efficiently, and then confidently return to production. This straightforward process takes just a few minutes but prevents unexpected startups that could harm both your valuable equipment and your workers. Think of it as a quick insurance policy that protects your most important assets
5. Keep up with maintenance
Regular servicing isn’t just good for production – it’s essential for safety. Set reminders for maintenance checks and keep detailed records. Think of it as a health check-up for your machinery that helps prevent unexpected failures that could cause injuries or costly downtime.
Keeping your machinery safe isn’t just about ticking a box – it protects your team and keeps your business running smoothly. Before starting work each day, encourage operators to spend just 5 minutes getting to know their machine. Look for anything unusual, listen for different sounds, and make sure guards are properly positioned. This small investment of time helps catch minor issues before they affect production quality, create delays, or cause injuries. Unsafe machines can lead to big fines. Take the time to get it right, and you’ll create a safer, more efficient workplace for everyone.
We’re excited to announce that HazardCo is officially expanding into the UK! As a New Zealand-born company, we’ve been helping builders and tradies keep their worksites safe since 2007. Now, after years of growth and success in both New Zealand and Australia, we’re ready to bring our trusted health and safety system to the UK market.
Why HazardCo?
At HazardCo, we’re all about making health and safety simple. We know that builders don’t want to spend their time buried in paperwork or worrying about compliance. That’s why we offer digital tools and expert advice to make health and safety easy to manage on-site, in real-time. Whether it’s inductions, risk assessments, or creating safety plans, our system takes the hassle out of health and safety, so builders can focus on what they do best—getting the job done.
Our journey so far
We started in New Zealand, helping Kiwi builders tackle their health and safety challenges. Word spread fast, and soon we had thousands of businesses using our system to stay safe. In 2020, we expanded to Australia, growing to 70 employees and over 10,000 members, including more than 150,000 users actively managing on-site safety through our app.
What’s next?
Now, we’re bringing the same proven system to the UK. We’ve tailored our offering to meet the specific needs of British builders, and our local health and safety experts are ready to provide the support you need. With the recent introduction of the Building Safety Act, there’s never been a more important time for builders to step up their safety game—and we’re here to help make that as simple as possible.
As the construction industry moves toward more digital solutions, HazardCo is ready to help UK builders stay compliant, protect their teams, and keep projects running smoothly.
Ready to take the guesswork out of health and safety? We’ve got your back!
The HazardCo App has a new Plant/Machinery Pre-Start tool! It’s a quick and easy way to do pre-start checks on various plant and machinery such as scissor lists, boom lifts and excavators. Just whip out your app, follow the guided prompts and you’ll know all your reports are saved for safe keeping.
This is a great new tool for those of you currently filling in the log book that stays with the machine, causing lots of painful admin work to gather and compile the information for your own records.
Why conduct pre-start checks?
Pre-start checks are a simple way to check your plant and machinery is up to scratch before it’s used. Whether it’s hired or owned equipment, a quick check will help you to find any potential issues that could impact on the safety of your team or the performance of the machinery. By referring to the manufacturer’s instructions and best practices, workers can make sure the machinery they have is in a safe condition to be used, and if not, the App gives you an easy way to communicate the issues happening on the ground to the right people. When done well pre-start checks go a long way to preventing incidents and equipment failures.
When to use the Plant/MachineryPre-Start tool
The Plant/Machinery Pre-Start tool should be used before the operation of any plant or machinery. You can find it in the main menu of the HazardCo App. Once a pre-start check is completed, the report is automatically saved to the Reports section in the Hub and the App for easy access in the future.
Bennefits for workers: The Plant/Machinery Pre-Start tool provides an easy way to follow pre-start procedures. It helps you to communicate any issues that need to go up the chain and make sure information isn’t lost or misunderstood.
Benefits for workers: This tool is a quicker and easier way to maintain evidence of your crews safe work practises on site. Anyone on site can use the app to complete a Plant/Machinerypre-start, you’ll be able to see it’s been done, and you won’t need to find and scan physical log books anymore!
HazardCo understands that on-site first aid is about more than just sending someone on a course every few years. As an employer or contractor on-site, you have a legal and moral obligation to make sure your team has access to first aid equipment and facilities, as well as access to trained first aiders.
To determine the necessary level of first aid for your workplace, assess the site by considering:
Don’t forget to involve your workers in the process, and if you are working with multiple trades, or are the main contractor, you should share information and work together cooperatively.
Having a kit on a construction site is essential to quickly address injuries and medical emergencies. Great first aid kits can be sourced from many places – a basic kit should at least include equipment to manage:
Basic first aid kits are not always enough given the nature of construction work and increased risk of eye injury, cuts, falls etc, so you’ll need to consider what other equipment to add e.g. eye pads, eyewash, additional dressings and bandages.
Include your team and see if they think your first aid kit is sufficient for the sites hazards and team size. Make sure they know who the trained first aider is and where the first aid kit is kept! Make sure your first aid kit is clearly labeled and is made from a material that can protect the contents from dust, moisture and contamination.
Lastly, assign someone to be in charge of replenishing the kit. Make sure this happens regularly and keep a list of what’s supposed to be in the kit to make topping it up easier. At the same time, check training is up to date for your first aiders, and if your team size has changed, whether you still have enough team members trained in first aid.
Keeping first aid up to date is the right thing to do by your team, so make sure you’ve got things covered and that you’re all prepared if any sort of injury takes place.
If you have any questions please get in touch with the HazardCo Team
WorkSafe recently published a report on Workplace harm and risk in New Zealand. The whopping 106-page report is packed with valuable information on the current state of safety and highlights areas that need improvement to create a safer environment for everyone.
Our certified Health and Safety Advisor Evette has pulled out all the stuff you need to know and provided advice on the safety areas you should focus on to make the biggest impact.
Most work-related fatalities and serious injuries happen in just a few industries. Unfortunately, construction makes the list, as does agriculture, forestry & fishing, manufacturing, and transport.
Over the past two decades, there has been a significant decline in the rate of fatalities and serious non-fatal injuries, with the fatality rate dropping by more than half. However, the pace of improvement has slowed down in the last ten years.
Between 2017 and 2021, New Zealand’s work-related fatality rate was still 40% higher than Australia’s, even after taking into account economic activity and employment differences. Although the comparison with Australia is worrying, it shows us there is potential to improve our fatality rates in NZ.
This graph shows the number of injuries that resulted in more than a week off work from 2022 to 2023. The injury rate accounts for the number of people working in the industry, rather than the total number of injuries.
Construction has the highest rate of all sectors. In other words, a construction worker heading out the door for the day has a higher chance of injury than someone working in a factory, driving a truck, working on a farm, or any other industry.
When we look at workplace injuries, we can group them into five main categories:
WorkSafe found that most serious injuries and deaths occur in just a few industries. To make these workplaces safer, it’s important to have strong safety measures in place. This means better safety rules (and enforcing them), providing proper training and resources for workers, and building a culture that values safety..
Here are some ways you can proactively create a safety culture on your site today:
Lead by example: Take the initiative in promoting safety. Regularly demonstrate safe practices and make safety a priority in your daily tasks. Your actions will encourage others to follow suit.
Encourage open communication: Create an environment where everyone feels comfortable discussing safety concerns. Encourage team members to share their thoughts and ideas on how to improve safety on-site.
Regular safety meetings: Schedule regular safety meetings to discuss any potential hazards, recent incidents, and preventive measures. Use these meetings as a platform to reinforce the importance of communication and teamwork.
Encourage reporting: Make it easy and non-intimidating for workers to report safety issues or concerns. Let them know their input is valued and will be acted upon.
Collaborate on solutions: Involve workers and contractors in finding solutions to safety challenges. By working together, you can come up with practical and effective ways to improve safety on-site.
Set clear expectations: Clearly communicate safety expectations and procedures to all workers and contractors. Ensure everyone knows their role in maintaining a safe work environment.
Evaluate and improve: Continuously assess your safety communication practices. Identify areas where communication might be lacking and take steps to strengthen it.
When we all understand the biggest causes of work-related harm, we can work together to create a future where every worker in New Zealand has a safe and healthy place to work.
For more information, you can check out our Fostering a Culture of Safety blog or download our Simple Guide to Toolbox Meetings.
The Ministry of Business, Innovation and Employment (MBIE) wants to hear about your experiences with the work health and safety system – how you think it’s working now, what you think works well, and what you think should change. We will be submitting our feedback and we encourage you to share your experiences too! https://www.mbie.govt.nz/have-your-say/work-health-and-safety